What is Float Deburring for Automation?
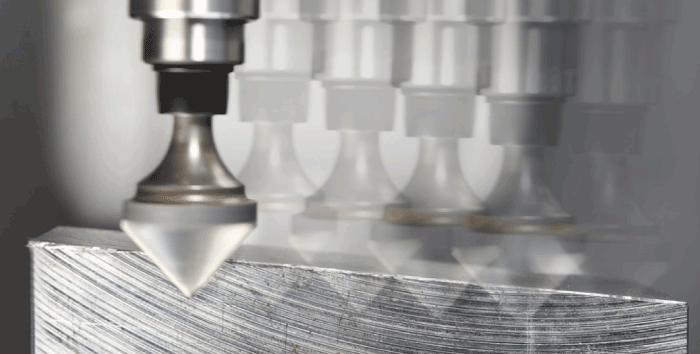
During machining of metal parts, unwanted protrusions called burrs often form, making the deburring process essential for quality production results. This process is often done manually which presents challenges including human error, the risk of injury, and quality requirements that need repeatability and consistency.
In addition, as manufacturing faces labor shortages the demand for automated deburring solutions continues to increase.
However, automating manual deburring with a machining center or robot may not always deliver the desired results. Several factors, such as cutting tool wear, variations in workpiece dimensions, and mounting errors, can lead to inconsistent burr sizes and shapes, complicating the automation process.
That's where Float Deburring comes in - Barriquan provides a machining method with a floating mechanism that aligns the tool perfectly with the workpiece's shape, preventing over-shaving and ensuring that no burrs are left behind. The tool maintains a consistent pressure along the workpiece, and self-compensates. As an effective automated robotic deburring option, it delivers precise and reliable results every time.
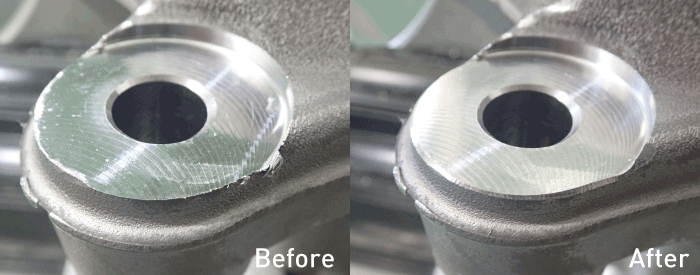
About the float mechanism and attachments
Barriquan excels at float deburring thanks to a radially compliant or axially compliant floating mechanism that uses springs and compressed air to push the tool against and along the workpiece at a consistent pressure. The mechanism is available in different configurations for flexibility - it may be built into a tool holder or spindle motor, or it may be an independent unit.
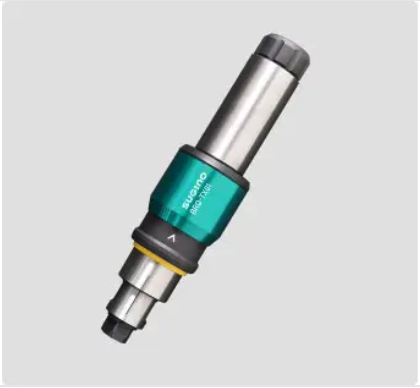
Tool Holder
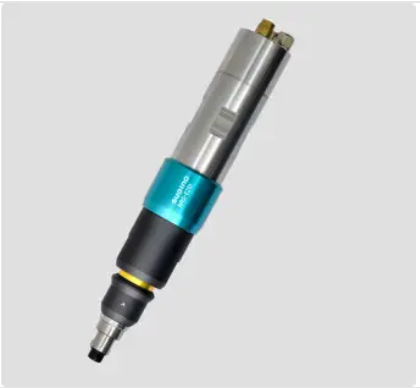
Spindle Motor
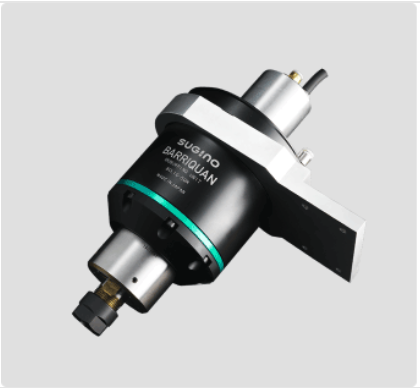
Independent Unit
Different Methods of Float Deburring
AXIALLY FLOATING TYPE
The axially floating type utilizes a mechanism that extends and retracts in the Z direction. It is ideal for deburring the edges of workpieces and is often used to deburr the contours of castings, and burrs that remain after machining.
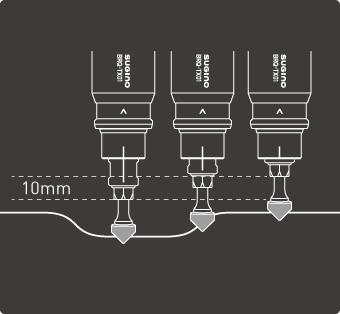
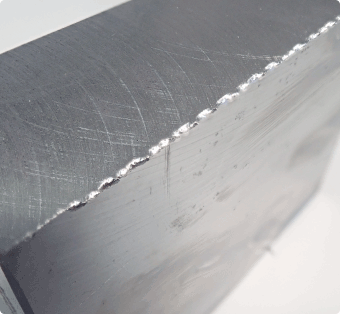
TILTING FLOATING TYPE
With this type, the tool is tilted to the workpiece. Suitable for protrusions and burrs that occur on the "surface" rather than the edge of a workpiece. It is often used for parting line removal of aluminum die castings, etc., and is mainly suitable for deburring using robots.
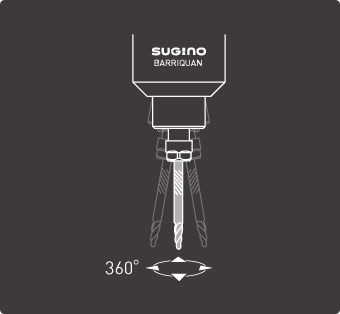
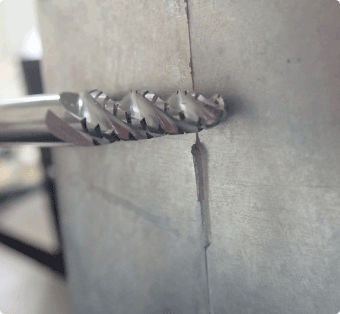
Manual vs. Automated Deburring: Human Judgement vs. Robotic Precision
One of the biggest challenges in automating deburring is replicating the human ability to perceive, judge, and apply a "knack" for the task. While vision cameras, sensors, and software can mimic human senses and decision-making to some extent, they struggle with processing ambiguous information as effectively as a human can.
Automated systems must go through multiple steps—inputting information, calculating, and then executing actions. This process can slow down deburring, especially when high-speed processing is required.
This is where the floating mechanism comes into play. It acts almost like an autonomic nervous system, responding to subtle, ambiguous variations without the need for conscious input. By directly reacting to these variations, the floating mechanism enables faster and more efficient deburring than what can be achieved with sensors and software alone.
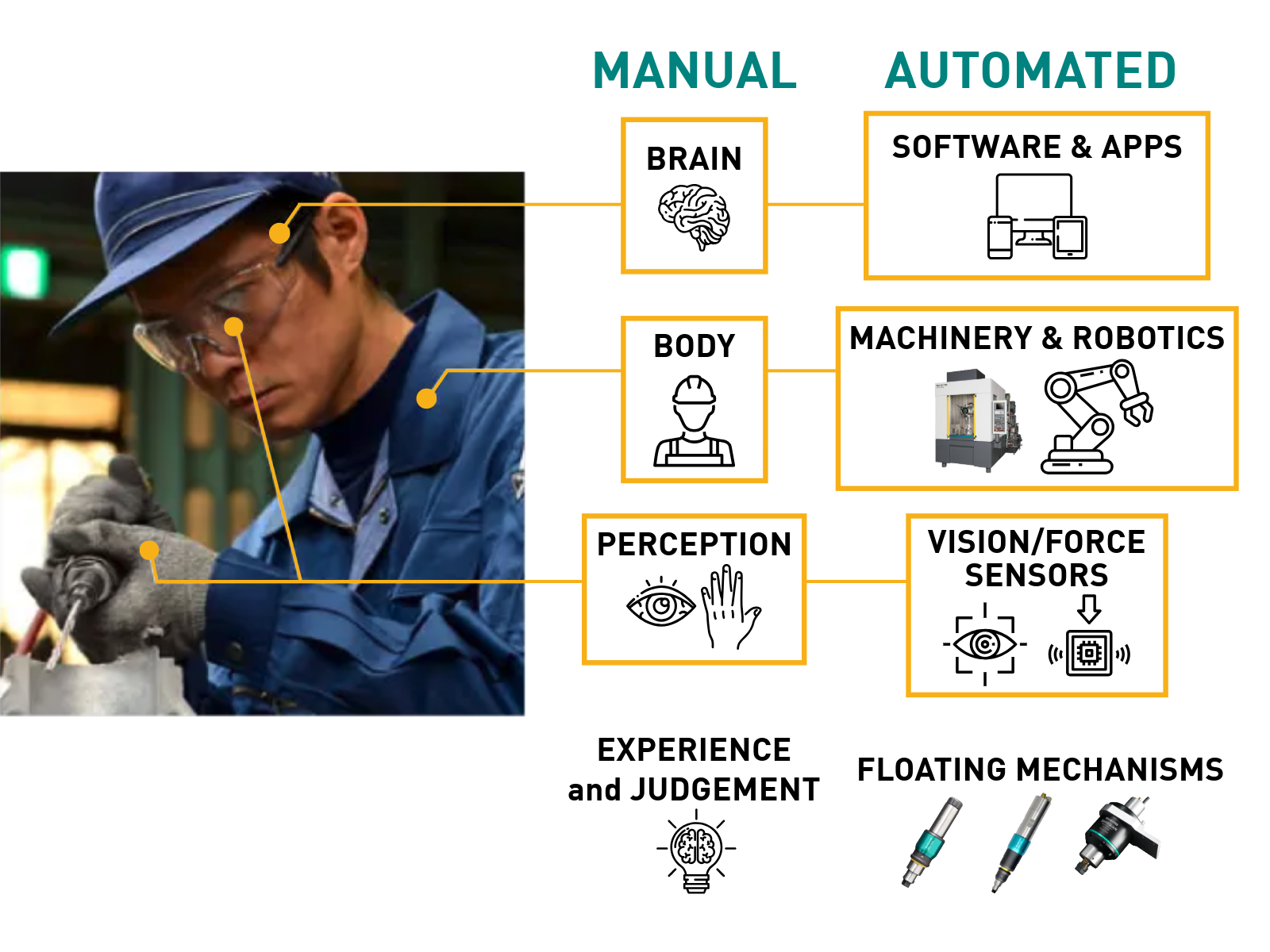
Articulated robots are widely used to automate transport and non-contact tasks, but are not suitable for tasks that require rigidity, such as metalworking.
As mentioned above, a floating mechanism can soften the load and impact on the robot, enabling automation of deburring even with a small multi-joint robot with low rigidity.
The floating mechanism also reduces teaching work and compensates for inaccurate trajectories, making it an excellent match for robot deburring.
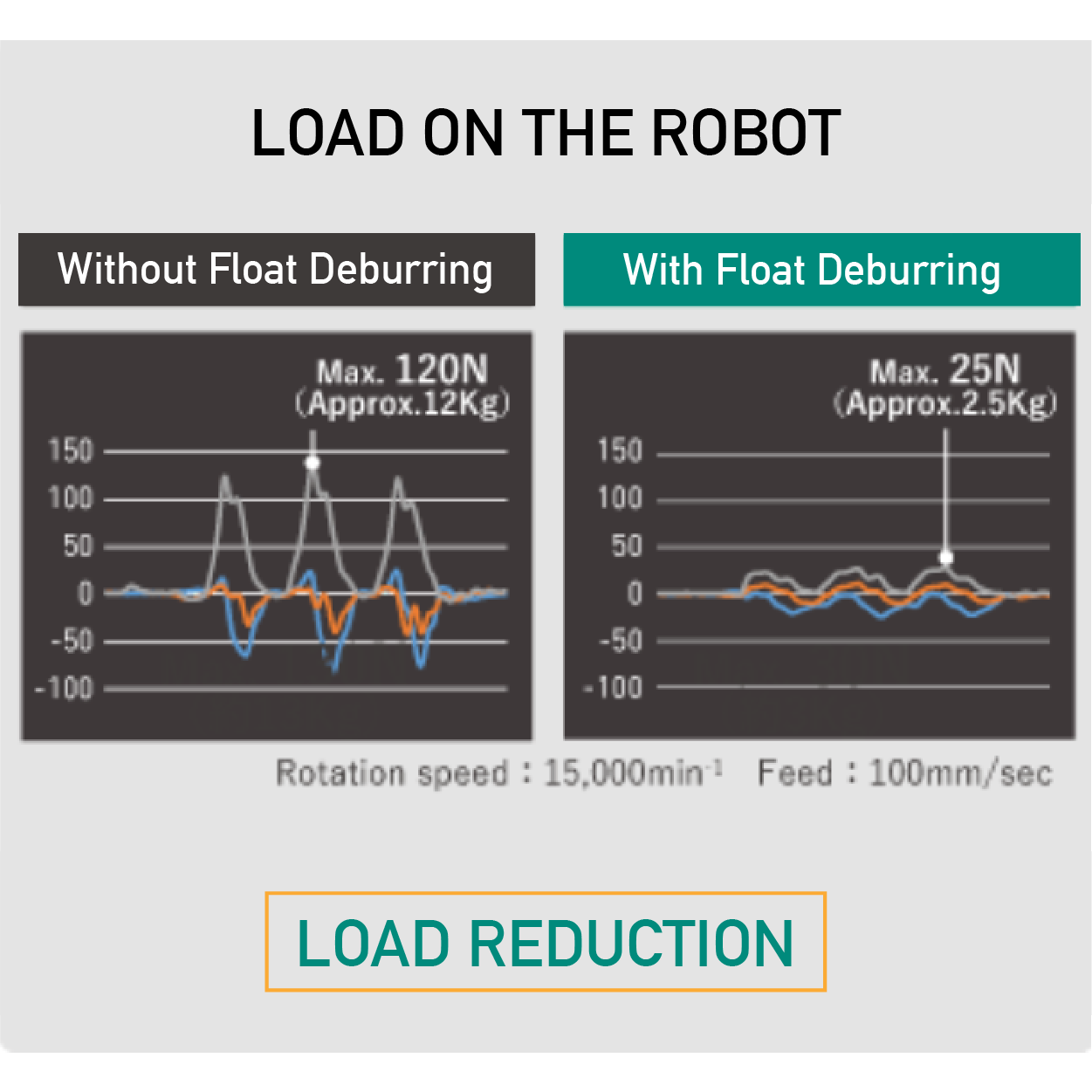
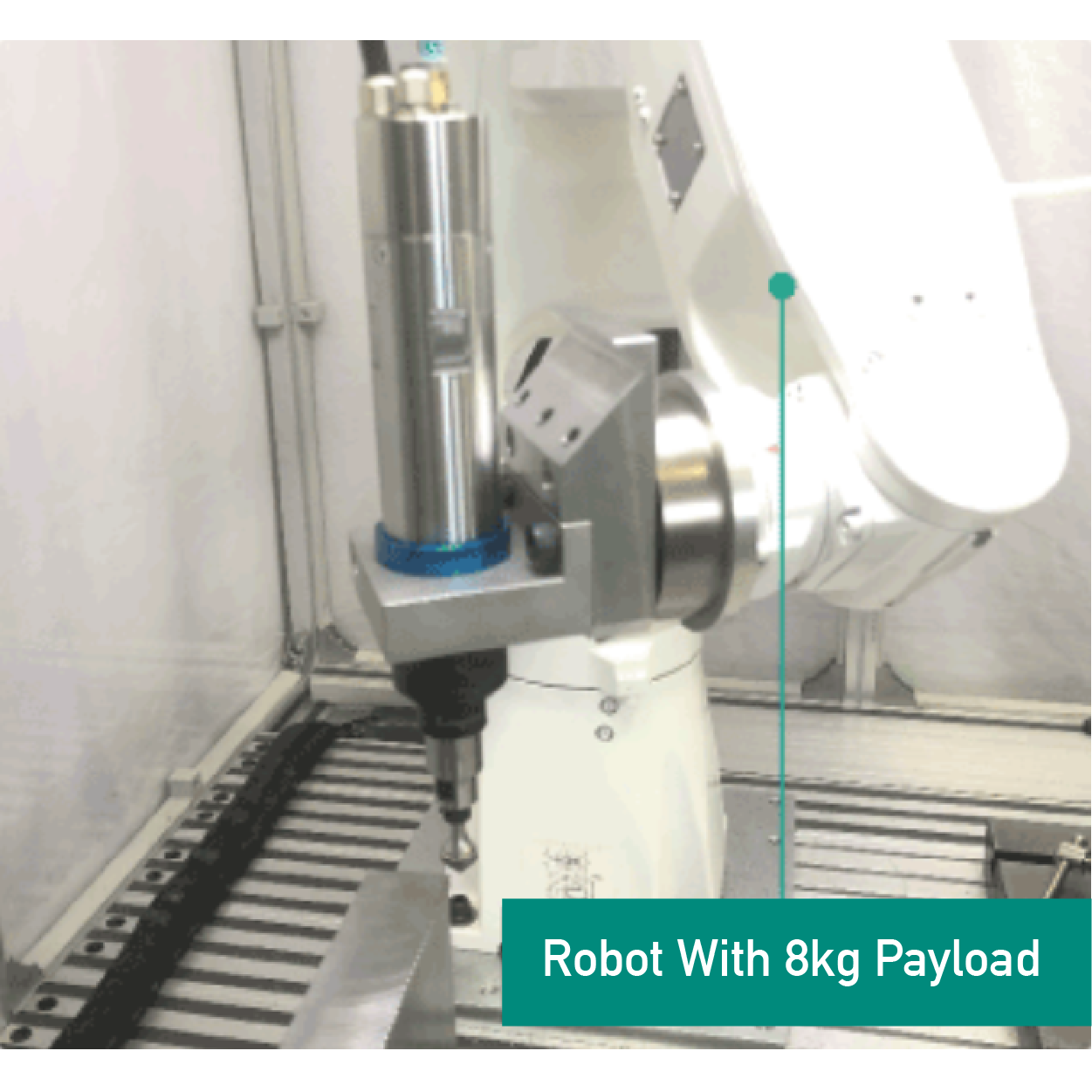
See it in action: watch how the different Barriquan mechanisms work
Axial Float Mechanism
The axially floating mechanism floats vertically and follows along both the workpiece’s height (Z) and horizontal directions (XY).
Height direction (Z direction)
Even if the distance between the workpiece and the tool and the tool's height changes, the tool stays with the workpiece due to the axially floating mechanism.
Horizontal direction (XY direction)
Even if the lateral distance between the workpiece and the tool changes, the tool follows the workpiece due to the expansion and contraction of the floating mechanism.
However, since the contact position between the tool and the workpiece changes, the distance that can be followed depends on the size of the tool.
The tilting mechanism tilts 360° and acts as a cushion where the tool meets the workpiece when approaching from any direction, as in robot teaching.
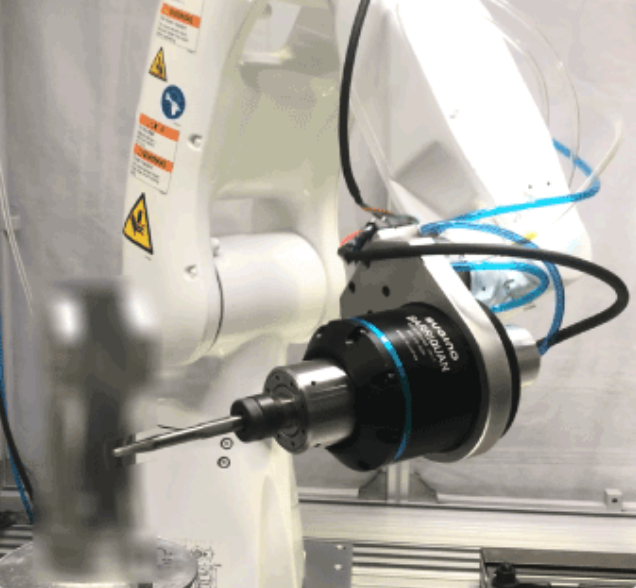
Cutter: A 90° angle at the tip is recommended
A conical carbide rotary bar with a 90° tip opening angle is suitable.
The use of sharp-edged cutters will shorten the life of the tool due to forces that prevent it from floating.
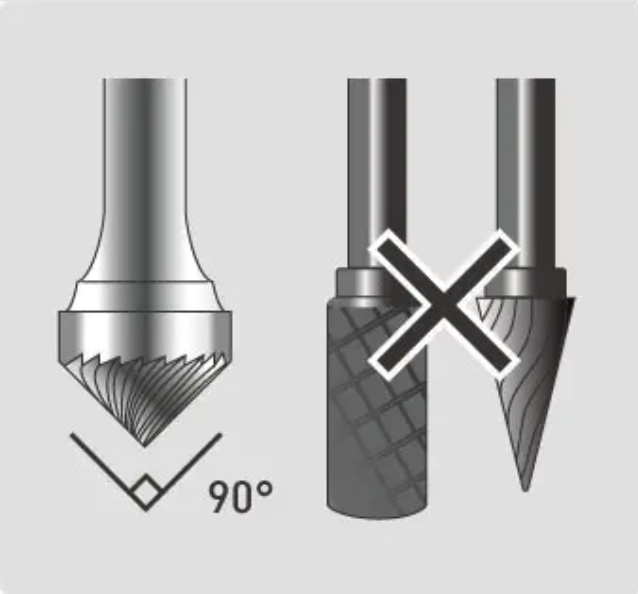
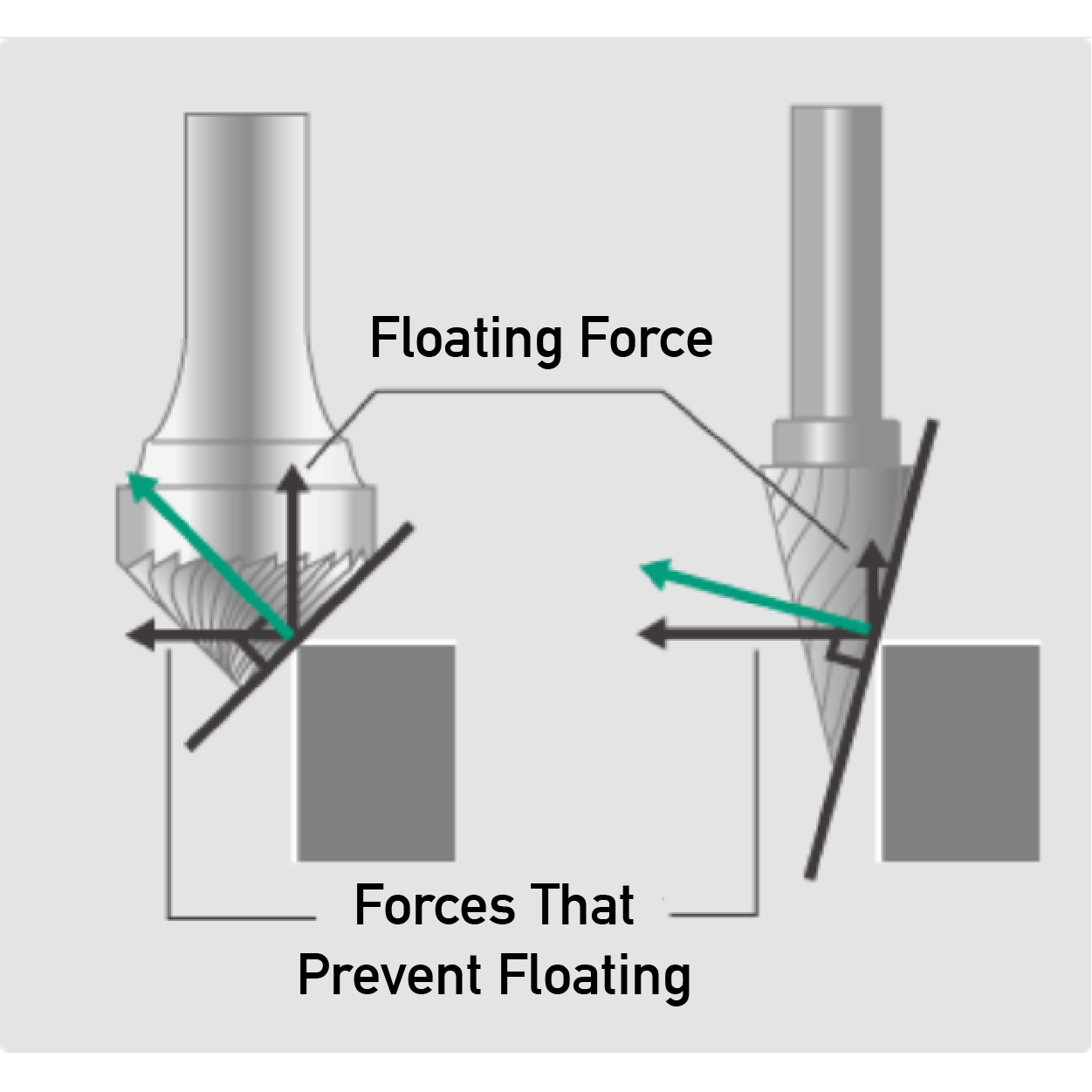
Cutter: The more blades, the better.
A cutter with a large number of blades is suitable for floating processing.
If the number of blades is small, the finished surface will deteriorate.
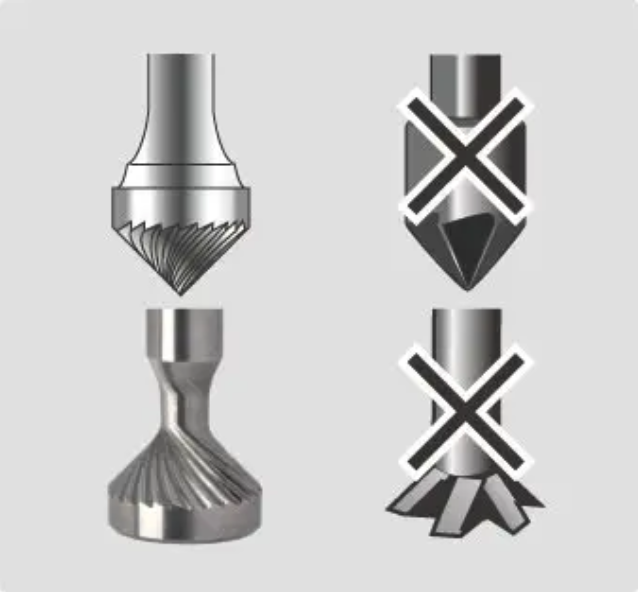
Brush: Bristles should have cutting power at the tips.
If the burr thickness is less than 0.15 mm, it can be deburred using a brush.
The floating mechanism allows the tip to extend as much as it wears, enabling stable deburring.
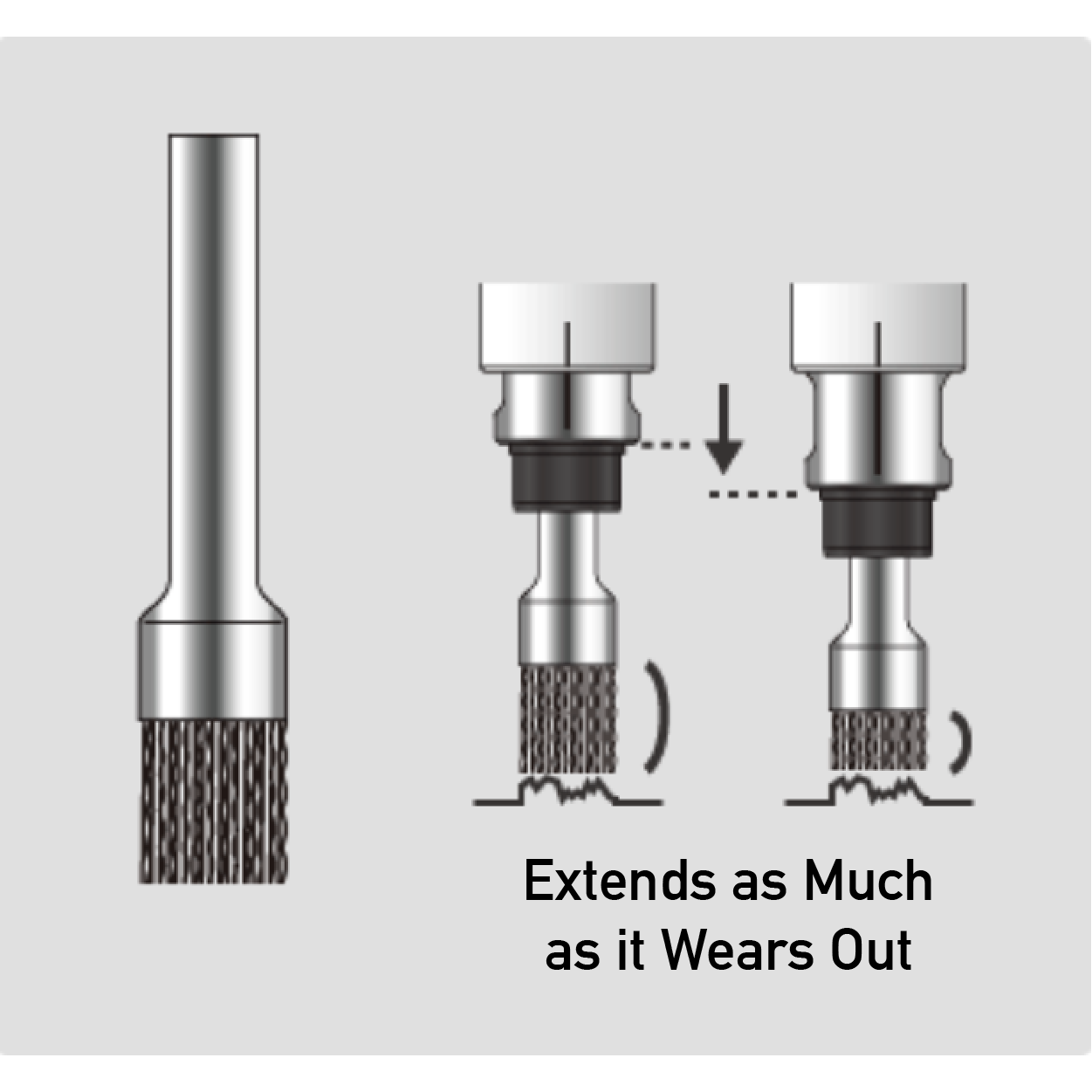
For Back Deburring
BARRIQUANC-BF01
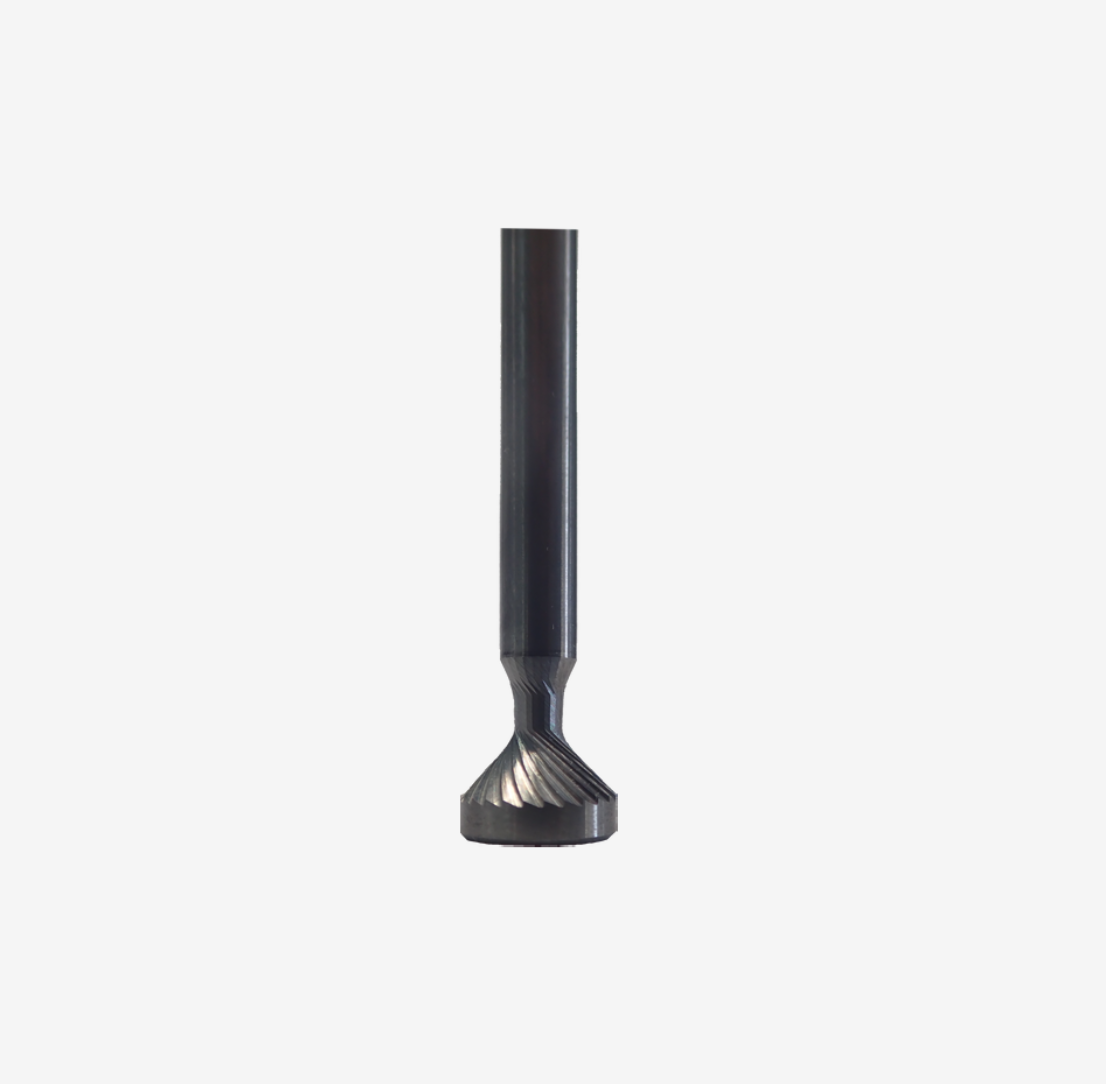