The portable, easy way to clean fine contamination and oils from your liquids.
JCC-HM Micro Bubble Fluid Cleaner / Emulsion Separator
Extend the fluid exchange cycle for cost reduction.
Improve quality with better workpiece cleanliness.
Protect system parts for maintenance cost reduction and fewer stoppages.
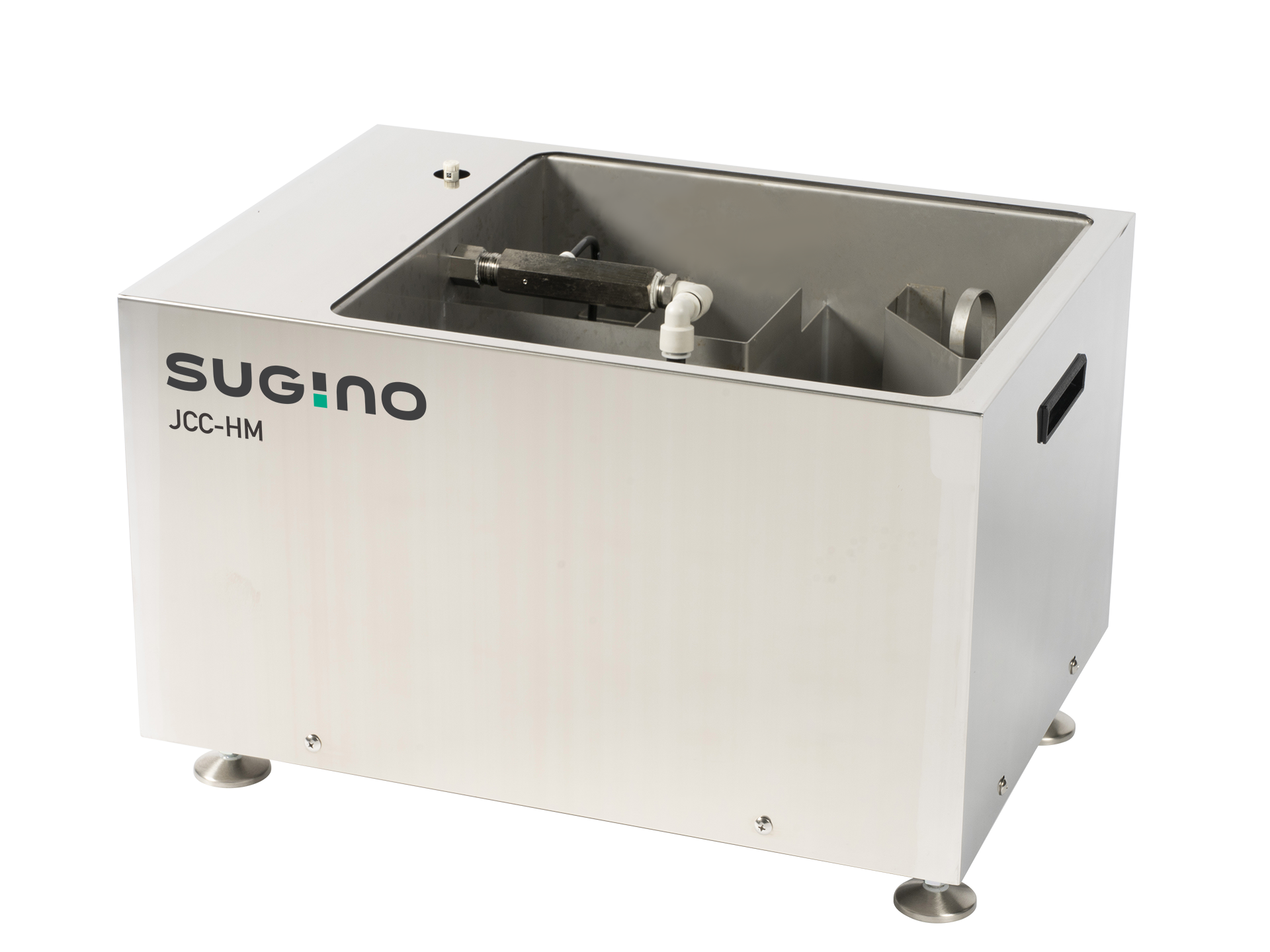
Increases water/coolant life and helps to protect important machine components such as pumps and seals
Aerates the fluid bath to help prevent bacterial growth and reduce foul odors
Helps to eliminate residue on finished parts and reduce the cost of fluid chemistry disposal and replacement
NOTE: Water soluble mixtures and emulsions may separate
Air is the Only Power Source Needed
Installation is simple and operation can start immediately. Preparation is complete after connecting just two hoses (IN/OUT) and air.
The JCC-HM is portable and simple to operate. The unit is compact, easy to move on casters, and requires only shop air to operate.
Watch it in action
Material | ADC transmission parts |
Equipment | High pressure washing machine |
Issue | Cleanliness deteriorates due to dirt in the cleaning liquid |
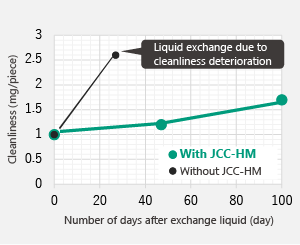
Example Two
Material | ADC parts |
Equipment | Machining Center |
Issue | Too many chips in the liquid, and sludge accumulates in the tank |
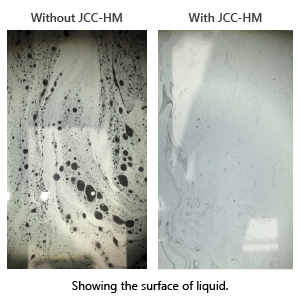
Micro Bubbles Remove Debris
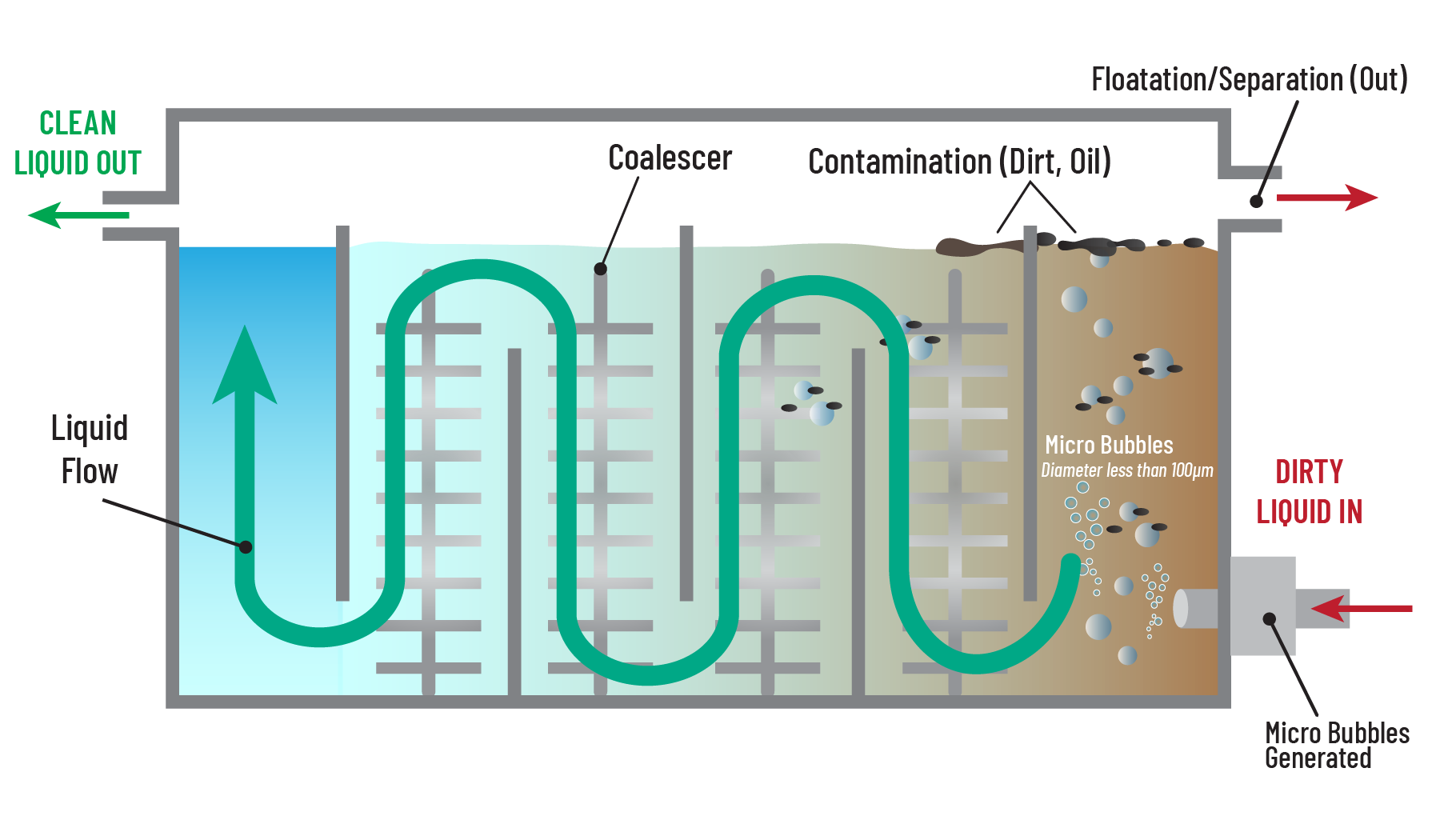

Specifications
Air Consumption
Noise
Dimensional Drawing (mm)
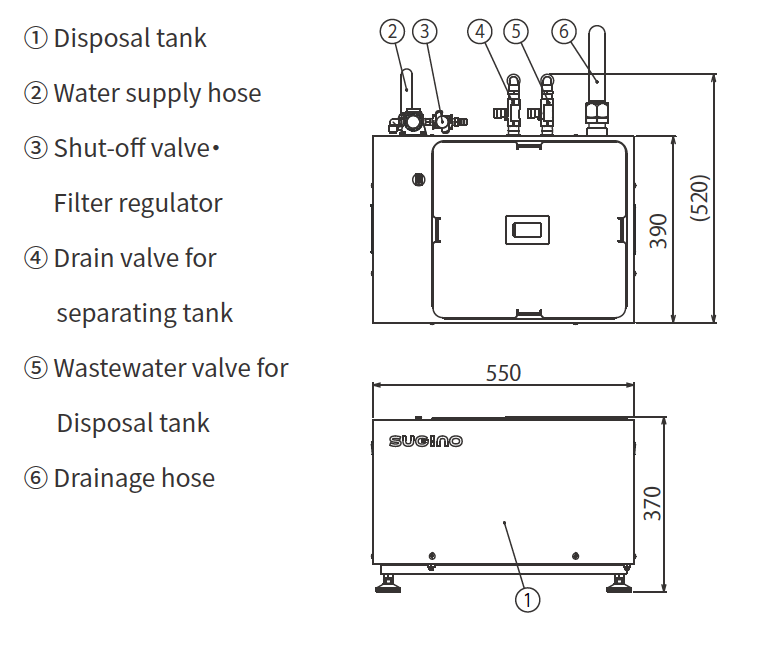
Have questions? Request a call or email and we'll help you get the answers.
JCC-HM Exclusive Optional Floating Oil Recovery Unit
Remove both floating oil and oil in the liquid, for better performance.
The optional floating oil recovery unit allows you to add even more functionality - simply connect it to the water supply of JCC-HM. If you are already using the HM, it can be retrofitted to recover oil from both the top of the liquid level, and within the liquid itself.

FEATURES
Recovering both the oil at the surface level and within the liquid, the JCC-HM doubles its processing speed to remove contaminants from your fluid tank.
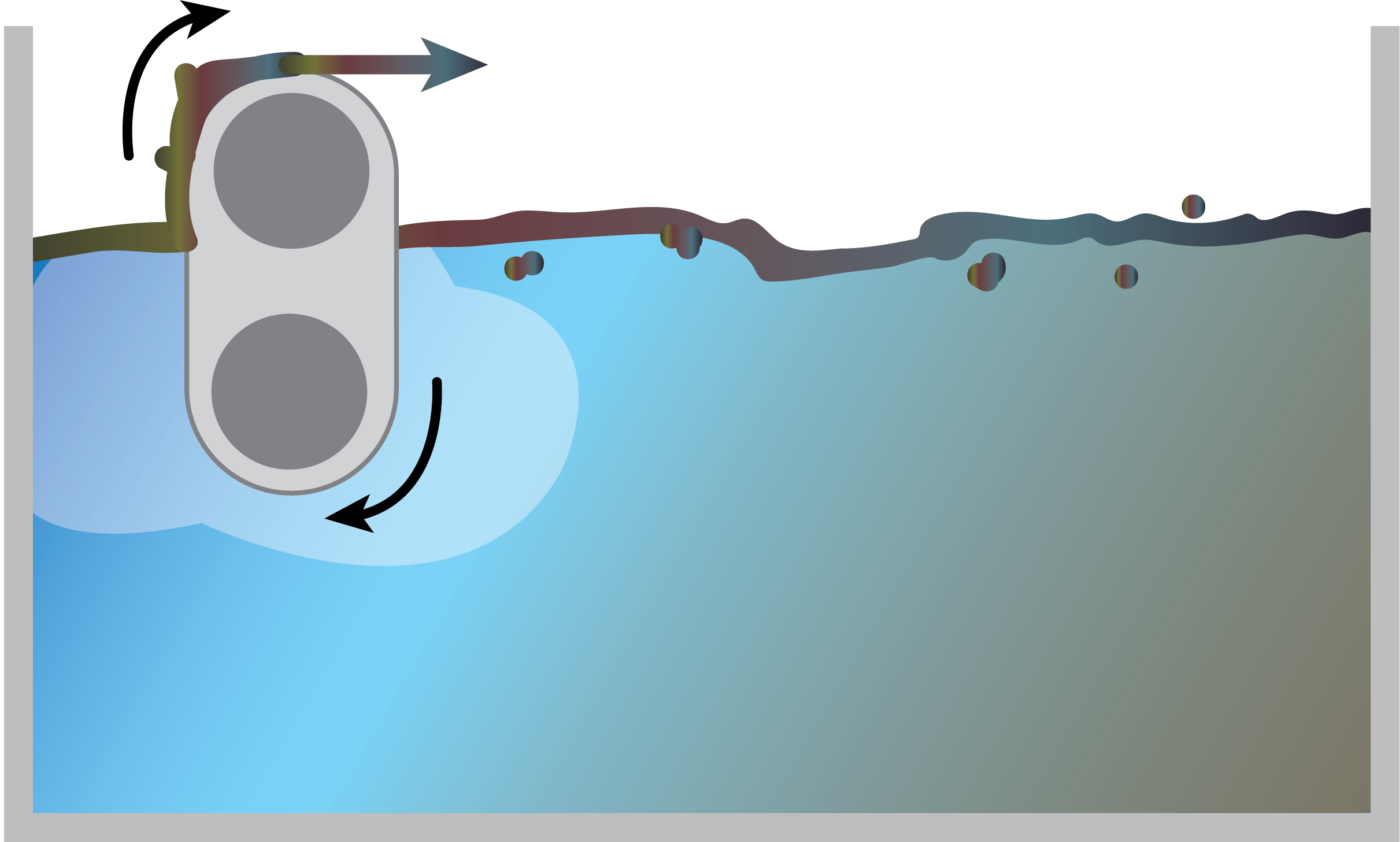
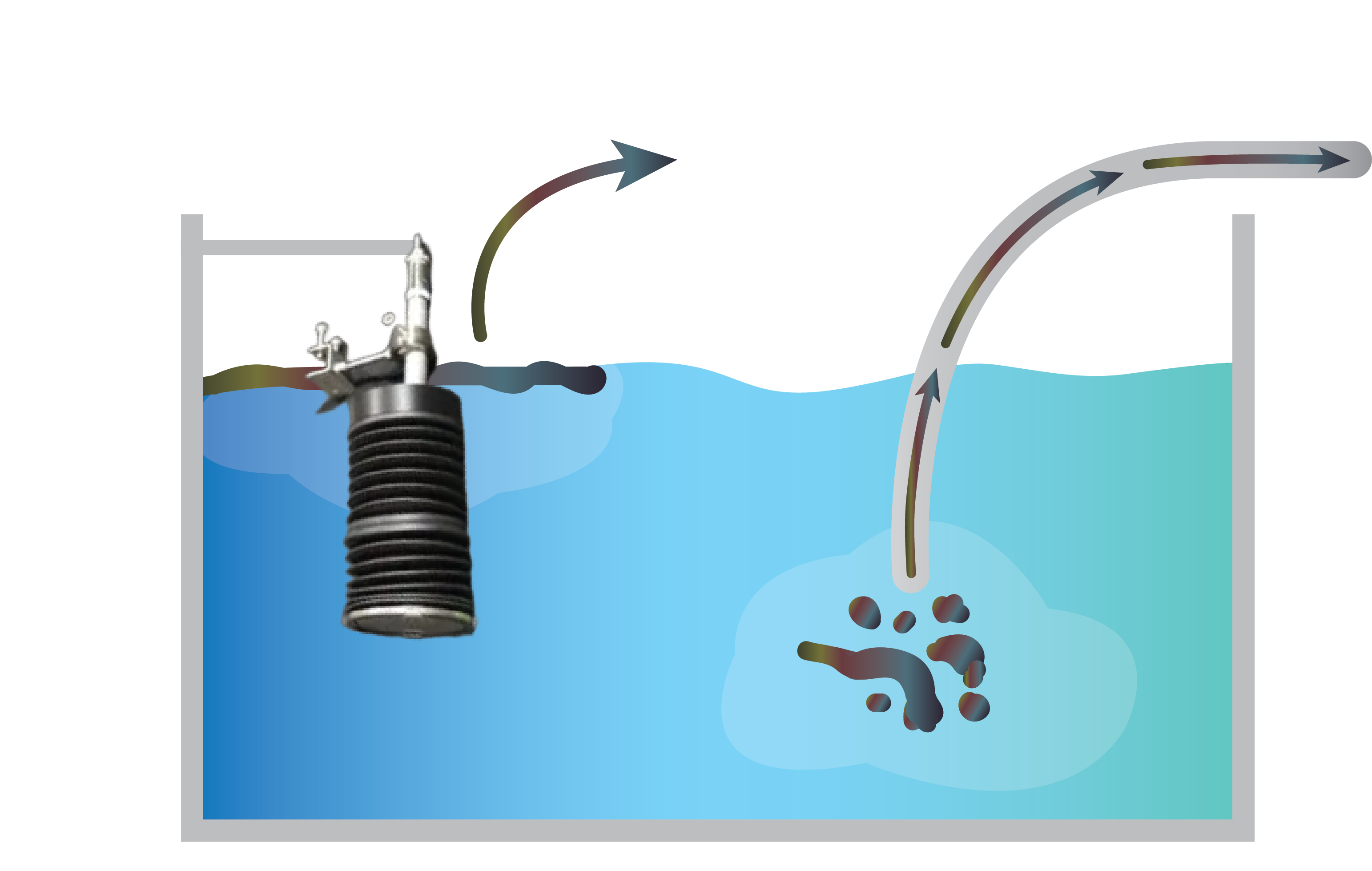
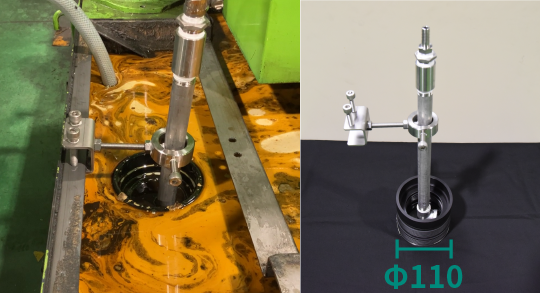
Fixes to the tank for stable operation.
In order to stably recover the oil in the liquid level, we adopted a method of fixing it to the tank. In the float type, it is affected by the fluctuation of the height of the liquid level, but by fixing it to the tank and installing it, it will continue to recover the floating oil stably.
In addition, the outer diameter of the unit is reduced to φ110, so it can be installed smoothly even in a tank with a small opening.
The bellows automatically follows the fluctuating level of the liquid.
The bellows portion of the unit can stretch up to a max. of 100 mm, maintaining an optimal position for stable recovery of floating oil at the surface of the liquid.
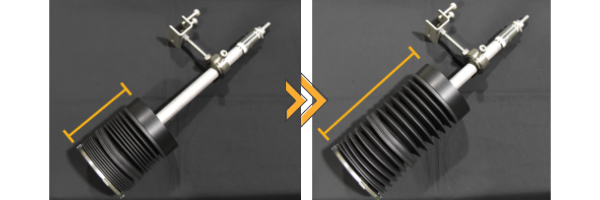
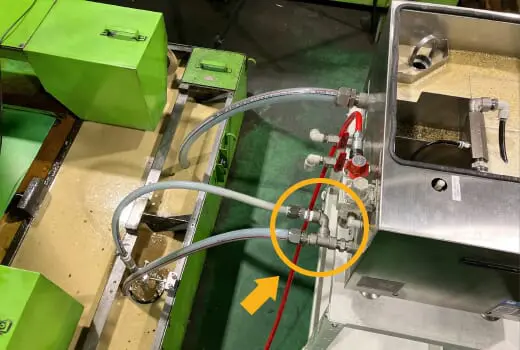
Designed to be retrofit to your existing JCC-HM, or added when the situation requires it.
The optional float unit can be attached to an existing JCC-HM processing circuit whenever you need it. Having it on-hand gives you the option to add it later according to the condition of the tank you want to process.
Case Study One - Grinder
Removes 97% of sludge in the liquid, preventing workpiece damage and poor quality.
Case Study Two - Brass Processing Equipment (Lathes)
Case Study Three - Reduction of Offensive Odors in Cutting Oil
Case Study Four - Oil Removal
Prevented spoilage and offensive odors in liquid - and
improved tool life and workpiece cleanliness.
Case Study Eight - Thoroughly Removing Oil in a Press Mold