Big parts need big ideas. Gigafeeder is purpose-built for drilling, tapping, and milling large aluminum die-cast automotive body structures and EV battery trays.
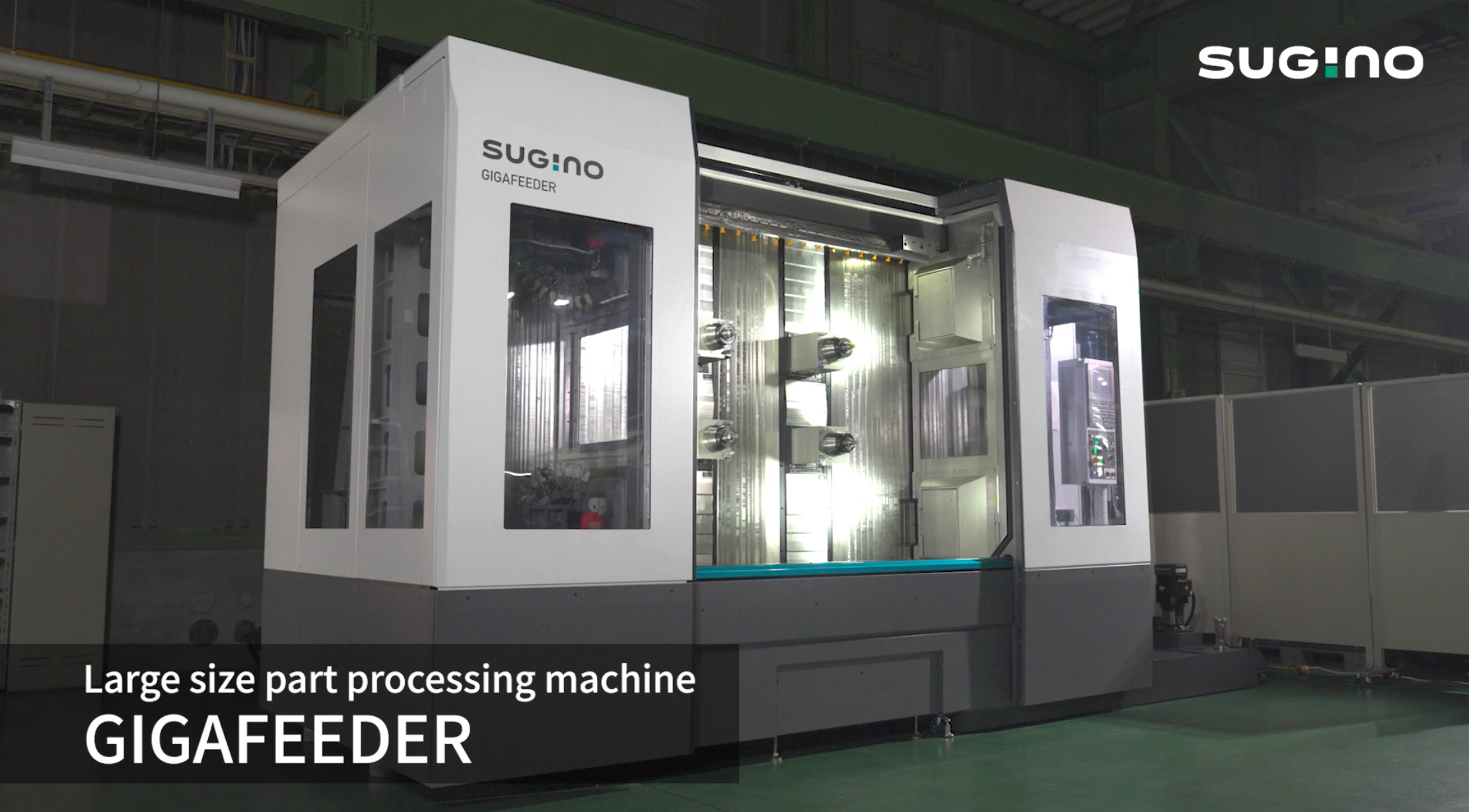
Gigafeeder is designed around – and builds upon – Sugino’s renowned Selfeeder drilling and tapping units and our highly rigid and accurate #30 taper spindle machining centers. A moving axis with a long stroke and ATC functionality are included for increased versatility.
Machining for Gigacasting, Mega Cast, and Large Components
Ideal for large parts — e.g. electric vehicle parts or aluminum gigacasting, die-casting, or mega cast auto bodies — that require extensive machining. Gigafeeder occupies a fraction of the floor space compared to conventional production lines.
Processing large parts or giga castings not only comes with challenges,
but these parts also need to meet the tight specifications you expect.
Meet tight cycle times, even for large parts.
Existing systems — such as large gantry and oversized machining centers — can accommodate large components. However, they aren't fast enough to meet the tight cycle times required in automotive manufacturing. But Gigafeeder is designed with multi-spindle capacity for simultaneous machining, and the rigidity and performance of a horizontal machining center.
Large parts don't have to rely on overly large machines.
Traditional huge processing equipment takes up an enormous amount of space. In contrast, Gigafeeder is designed to occupy far less space compared to conventional production lines, but still offers a wide/large processing area. And flexible modules work a variety of ways (index, conveyor), and are easily repurposed as needs change.
Get to know Gigafeeder,
and then get expert insight.
MORE TOOLS FOR MORE PRODUCTIVITY.
Equipped with ATC for flexible machining
Each spindle comes equipped with an ATC magazine that holds up to 11 tools. In addition to drilling and tapping, flexible processing such as milling can be performed.
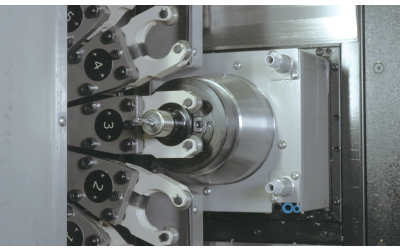
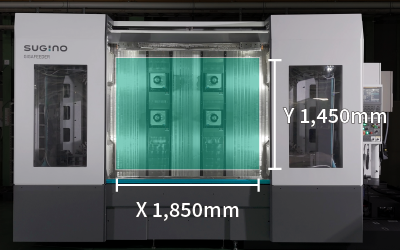
BIG RESULTS
Spacious processing area for large parts
The four horizontal spindles installed as standard have a machining area of 1,850 mm on the X axis, 1,450 mm on the Y axis, and 350 mm on the Z axis, ensuring sufficient stroke for machining large EV parts, battery trays, and the like.
LESS PROCESSING TIME
Simultaneous machining of multiple locations using #30 taper spindles reduces machining time
Gigafeeder is equipped with 4 spindles as standard (up to 6 spindles). Each module performs machining at the same time using separate operations, significantly reducing machining time. For example, by combining multiple modules using the index method, it is possible to shorten the process time even further.
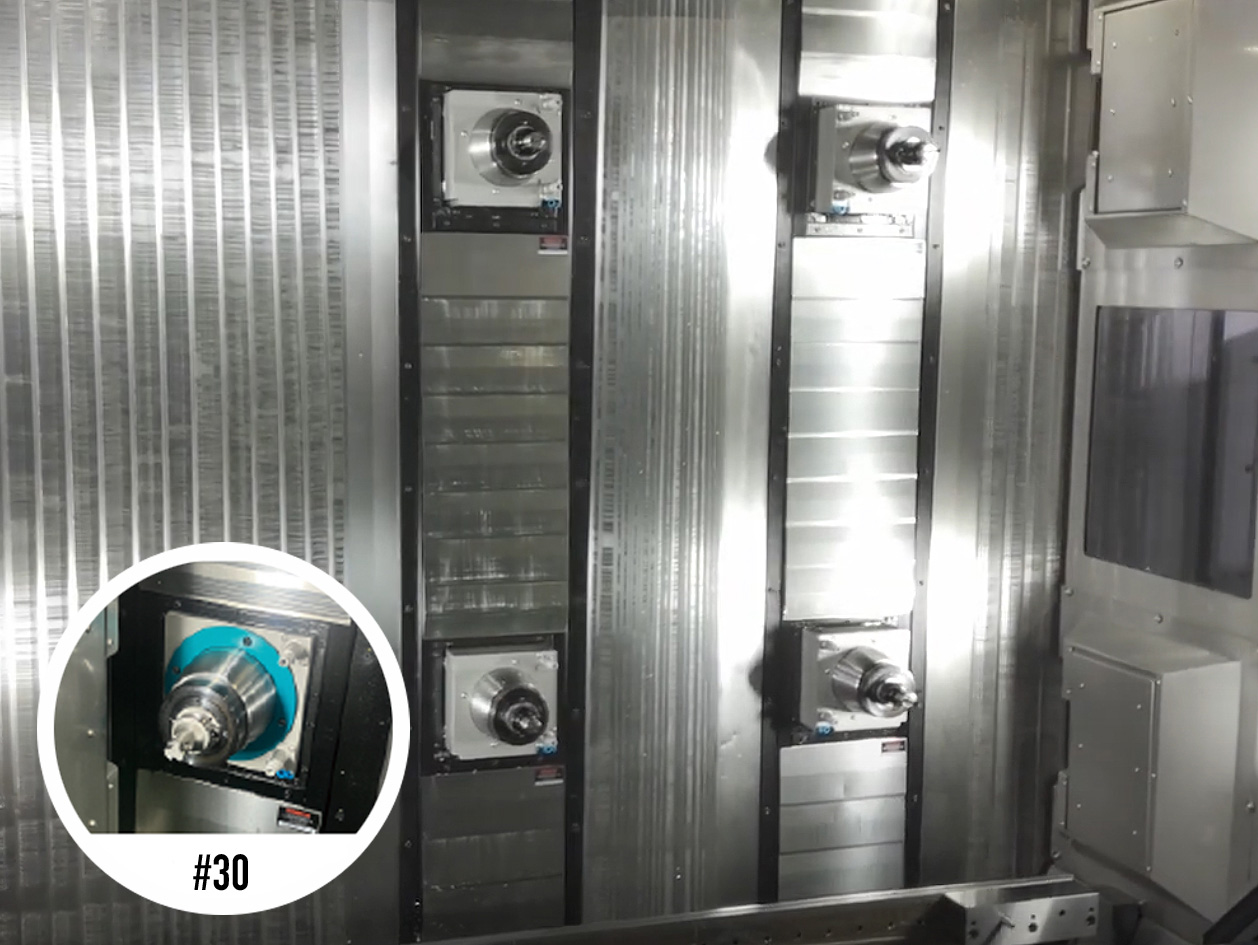
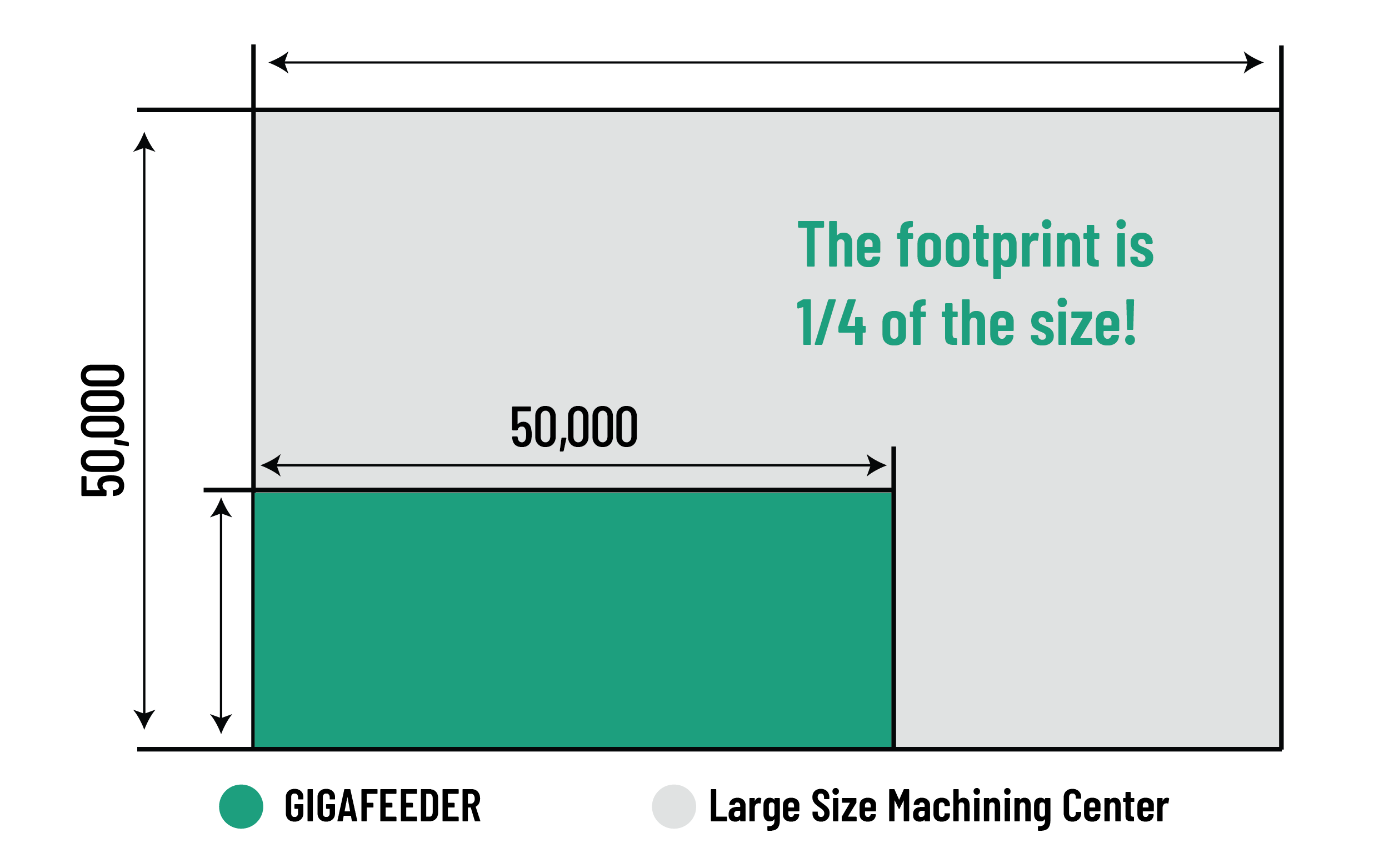
SMALLER FOOTPRINT
Minimize your production line with space-saving design.
The main axis of Gigafeeder is installed horizontally, and the workpiece is attached to a tombstone and processed like a horizontal machining center. Comparatively, the footprint is surprisingly small compared to gantry machining centers and large vertical machining centers with similar machining areas. Additionally, this design allows for efficient use of space without sacrificing machining capabilities.
Create your optimal line layout by setting up modules in a
variety of configurations, ensuring flexibility and customization.
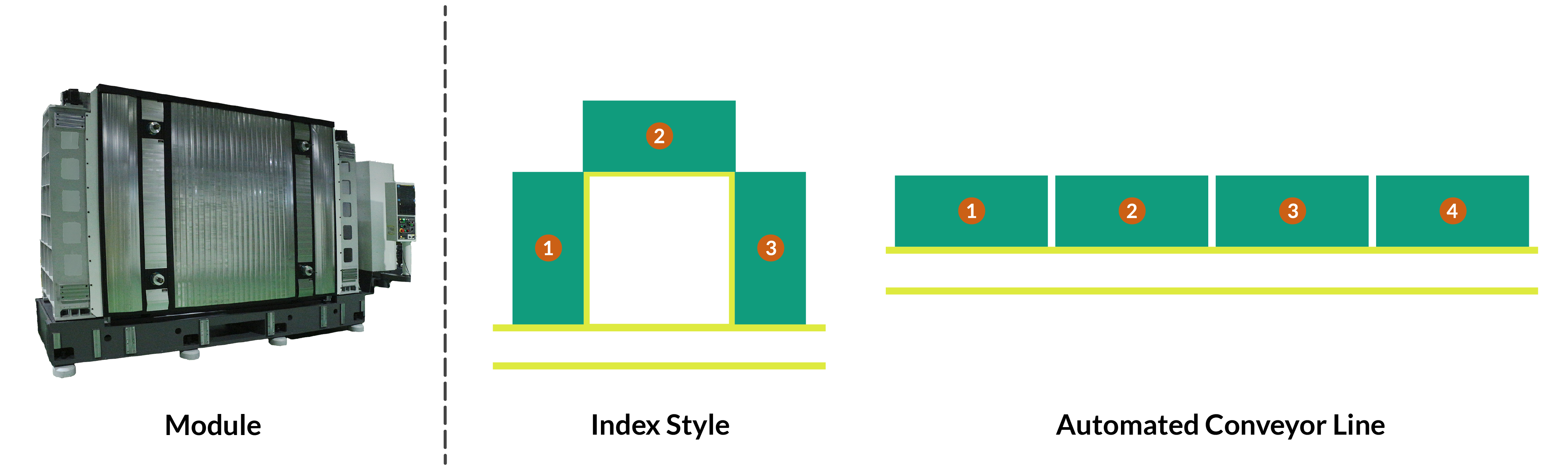
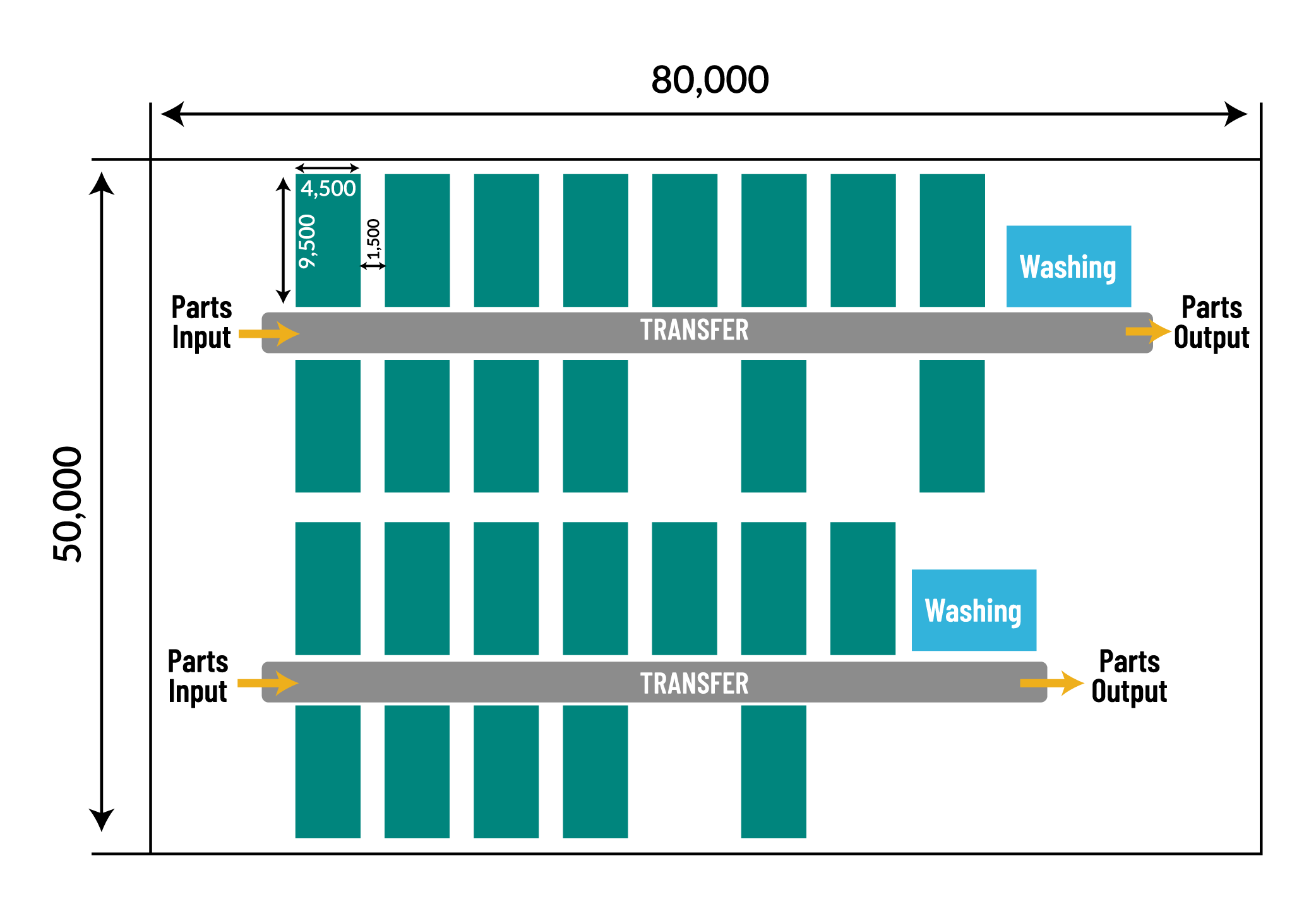
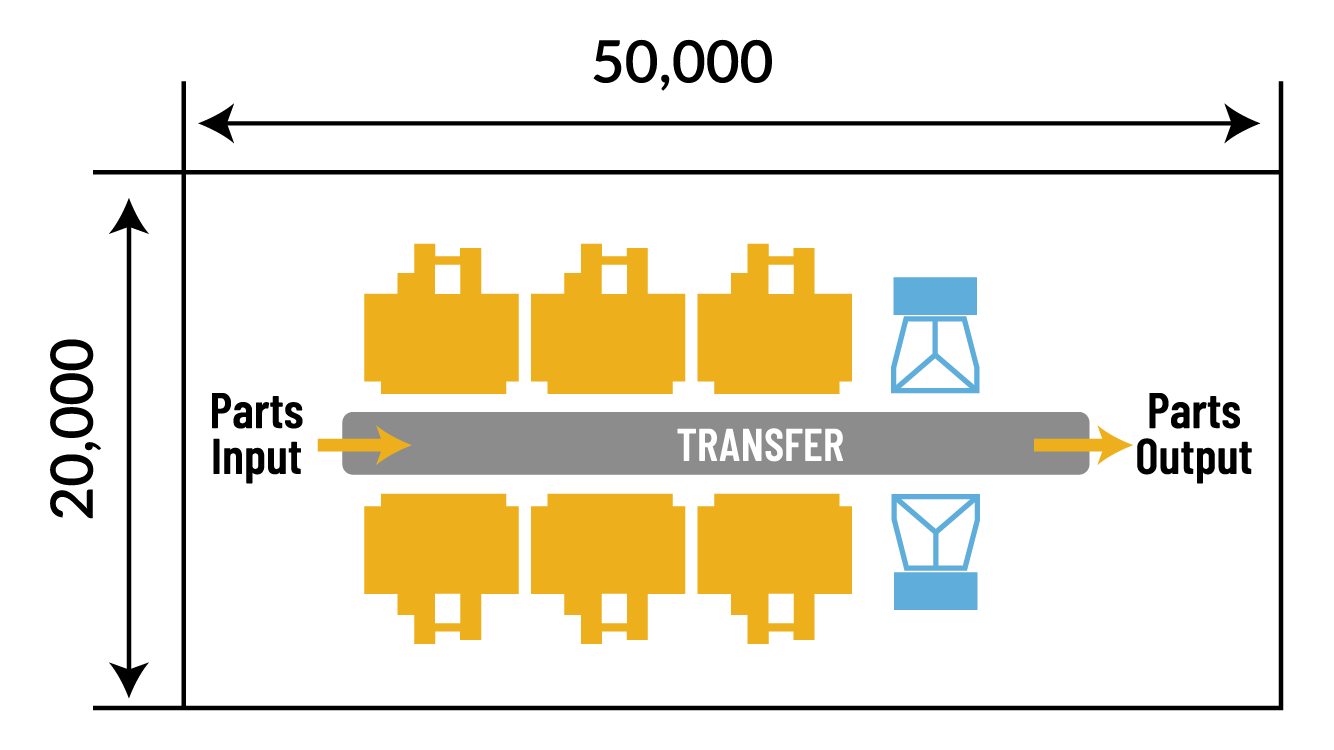
Large Machining Center
Required Space: 80 x 50 = 4,000 m2
Required Machines: 26
Required Space: 50 x 20 = 1,000 m2
Required Machines: 6 sets of 4 stations, index-style machines
*Total length of device body excluding coolant tank: 4,100mm
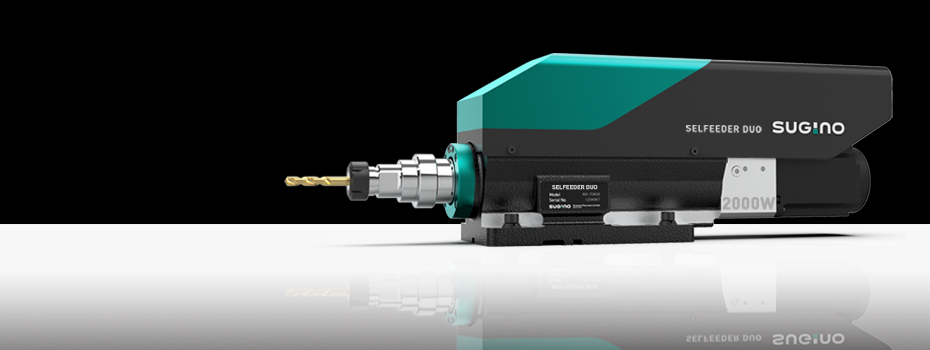
The flexible, drilling and tapping powerhouse: Selfeeder Duo
Selfeeder x Robot
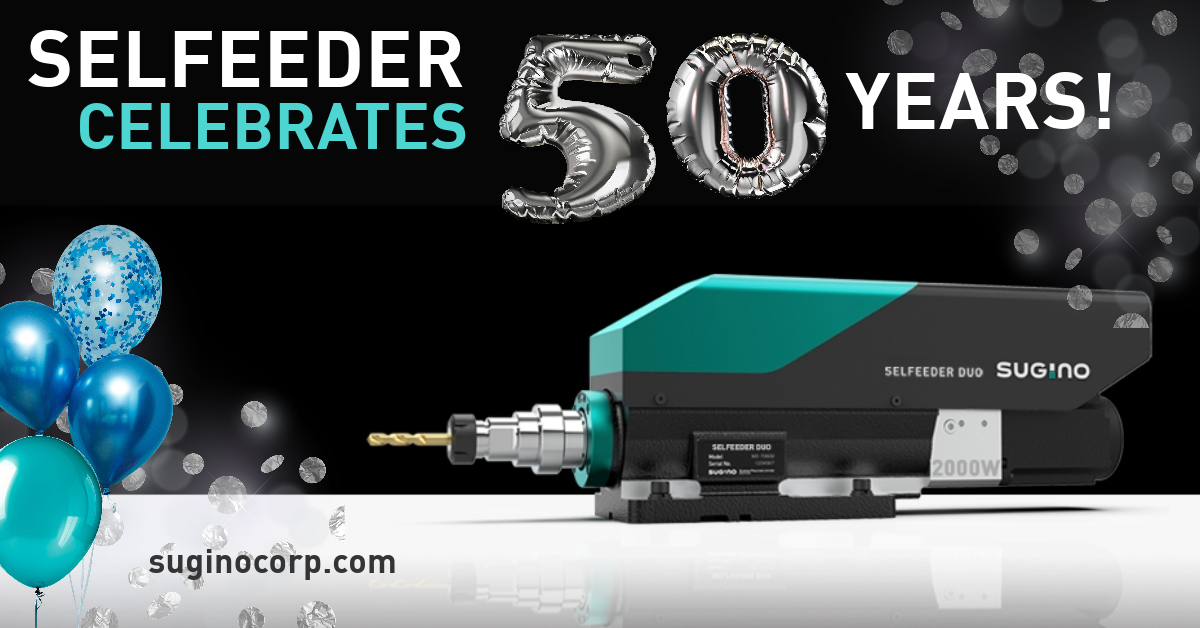
50 Years of Selfeeder
2023 marked the 50th anniversary of the Selfeeder Electric Series, one of Sugino’s line of drilling units, which along with Synchrotapper are global standards for drilling and tapping.