Get to know the nozzles and pumps inside a CNC deburring and parts cleaning system to learn how they impact your results.
There are two main components to any effective CNC high-pressure cleaning and deburring process: the pump and the nozzle(s). The pump provides consistent, yet variable pressure with the appropriate fluid flow. The nozzles focus pressurized fluid to the right spot to produce the desired results you want – whether it be cleaning, deburring, or both.
The pump and the nozzle(s) work together in a CNC environment to provide the necessary direction. The pump is controlled via a servo motor to vary the water pressure as programmed and the nozzles are programmed to the exact spot(s) required.
With CNC high-pressure water deburring (HPWD), a high-pressure waterjet is directed along edges and specific part features to selectively deburr surfaces. The primary benefits to this type of system are it’s precision, control, and repeatability.
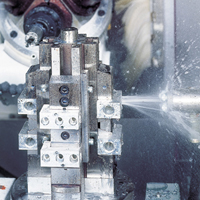
Sugino has a decades-long history of harnessing the power of water.
Most high-pressure CNC cleaning and deburring units typically operate between 5,000 and 10,000 PSI*. However, Sugino offers models that can run up to 36,000 PSI for hard metals like Titanium, Stainless Steel, and Inconel. With a wide range of pressure options, comes a broader set of options to fit your specific production challenges, cycle times, or cleanliness specs. It’s just another way to dial-in your program for great results.
Nozzles for Effective Deburring and Cleaning
The nozzle is the other key to the high-pressure cleaning and deburring process. There are a wide variety of nozzle options available and in many cases, multiple nozzles can be used throughout the cleaning or deburring of a part
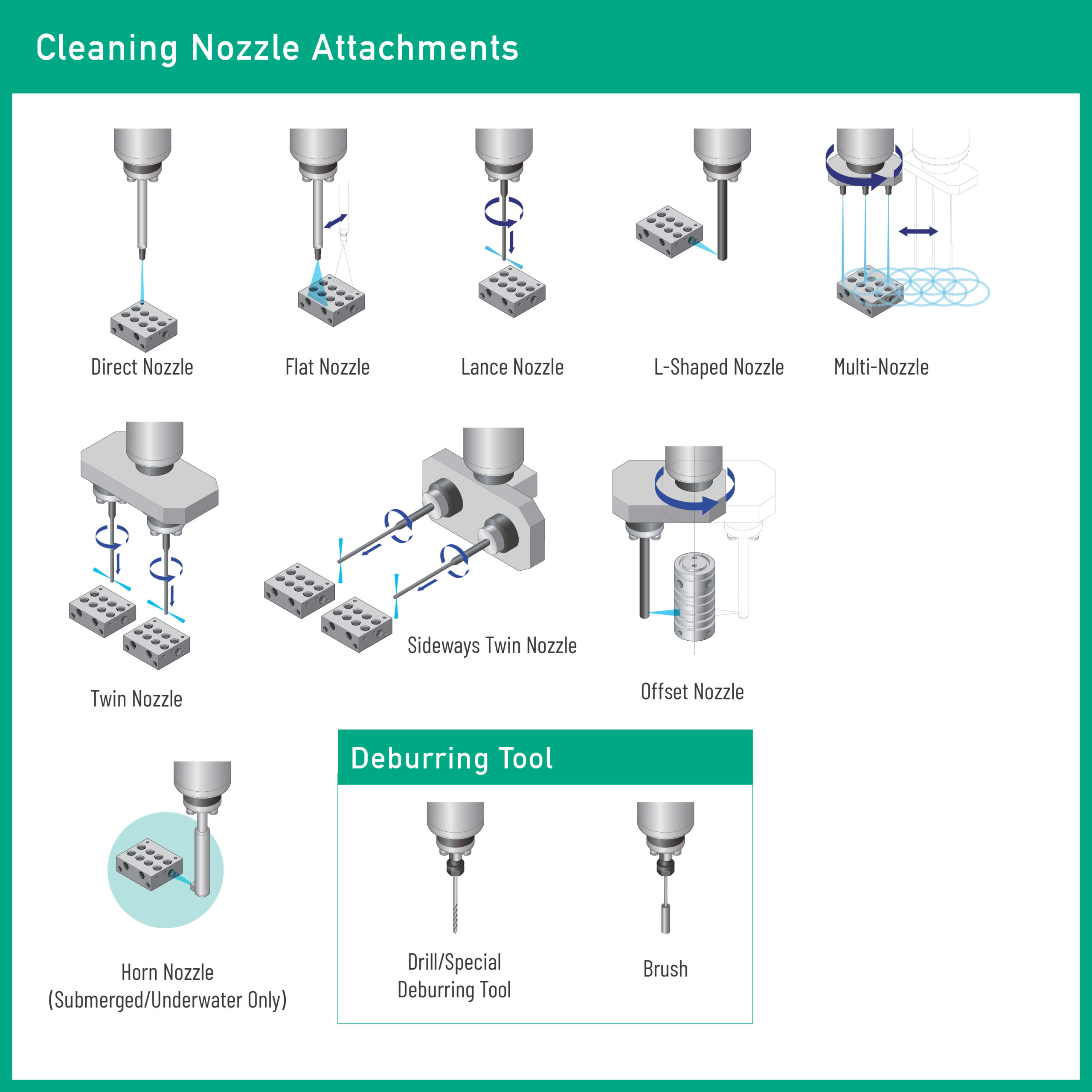
This image shows the broad variety of nozzle types available from Sugino for CNC deburring and parts cleaning.
Nozzles come in many types, including direct, flat, rotating, probe or lance, L-type, angled, and offset. Dual nozzle set-ups can be added to process two identical parts at the same time – thus doubling the production output in the same cycle time. Fluid flow is split between the nozzles, but the required pressure is maintained.
Understanding the capabilities, pros and cons of these options will give you an informed basis to find the right solution for your production challenges – and help you achieve your desired results.
Footnote: * Bertsche, Richard W. “Why Use Waterjet Deburring?”, SME.org, August 1, 2007, https://loom.ly/xy9Kb9Y
Did you miss last week’s installment on CNC and the different axes? Catch up here.
Need a collaborative partner to help you brainstorm solutions for high-pressure water deburring and/or parts washing? We have a decades of experience that help us, help you. Get in touch to start a discussion.