Last week we spent some time covering the identification of burrs. Why? Because classification of burrs can help you pinpoint the best removal processes and prevention methods.
This week we look at the classes burrs fall into. Burrs come in many types, and they can then be categorized in several different ways. They can be sorted by machining process, machining method, position (inside or outside), or material.
Additionally, burrs can also be grouped by size, root thickness (how they are attached to the main structure that is machined), and ease of removal. As shown below, in this classification system, there are essentially five types of burrs:
Burr Classes

Burr classes as shown in Production Machining
Class 1
Micro-burrs that can only be seen by magnification. They appear as sharp edges to the naked eye.
Class 2
Feather burrs that can be seen without magnification and are characterized by extremely thin roots. These are removable by the tip of a pencil or fingernail.
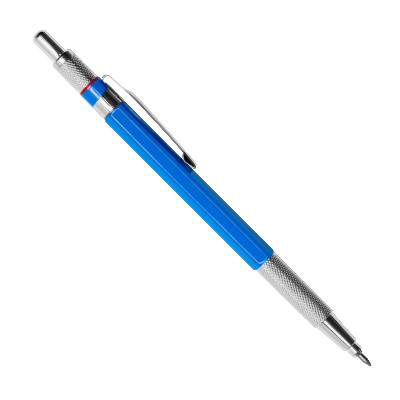
The pencil test is one method of determining the root strength of your burrs.
Class 3
Well-attached burrs that are relatively small. Despite their size, significant mechanical energy must be applied for removal.
Class 4
Like Class 3 burrs, these are well attached. The primary difference is they are larger and have a greater root thickness.
Class 5
Very large, extruded burrs with thick, rigid roots. Brushes can sometimes remove Class 5 burrs, but they often require a stock removal operation such as grinding or machining.
Note: These standards are generalized and classification will vary based on material and cleanliness specifications.
Knowing Your Burr Leads to Better Decisions
To sum it up, understanding which class of burr you are dealing with helps you determine the best way to remove them. Qualifying burrs based on their characteristics provides insight into how to tackle them for your production process and desired results.
LaRoux Gillespie – often recognized as one of the foremost experts on the topic of deburring – gives us a better explanation of all the factors that lead to a solid deburring plan:
When determining which one is most effective, shops must assess a variety of factors, including the burr height and thickness, workpiece material, allowable edge radius, maximum stock loss in the surrounding area, required surface finish, and, of course, the number of parts that will be produced and therefore the economics,” he said. “For many of today’s commercial products, any negative effects of the deburring process are small enough that they can be ignored, but for precision parts, it is essential to evaluate these impacts early on in the manufacturing planning stage. ¹
Next week we will start to delve into the many options of deburring.
[¹] https://www.sme.org/technologies/articles/2019/december/sizing-up-deburring-operations/