Burrs are not “one size fits all.” The types of burrs vary with machining processes and methods – and they come in just as many different types.
Just joining us? Take a look at last week’s Deburring 101: Reasons Deburring is Crucial
Identifying the type of burrs you are dealing with allows you to address not only the removal process, but ways of preventing them from forming in the first place. Examining the characteristics of burrs will provide information that helps you find the best deburring solution.
To illustrate the point, the chart below provides some examples of burrs and their relation to specific machining processes.
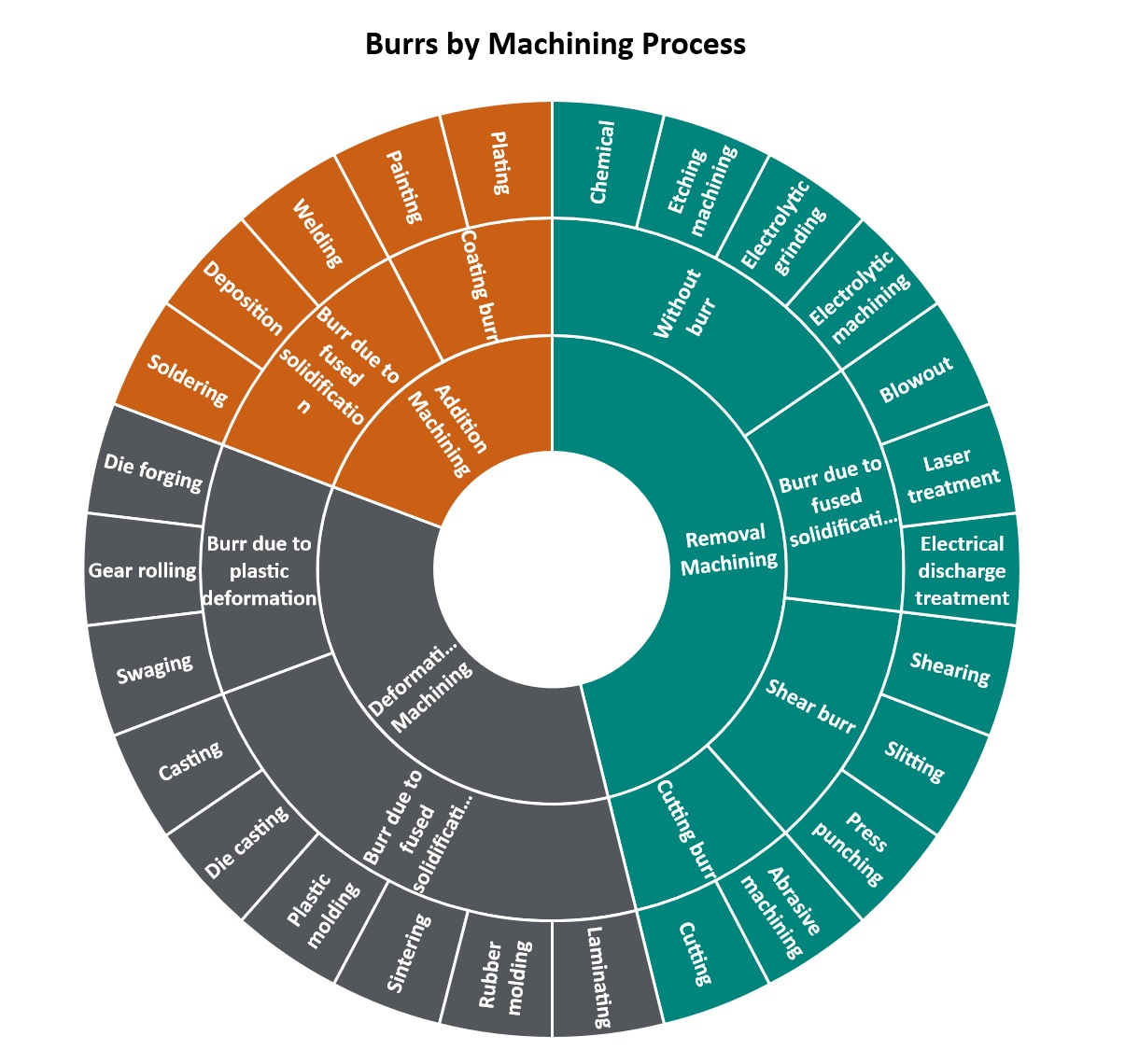
Types of Burrs by Machining Process
Subgroups of Burrs and What They Look Like
Next, we can break down types of burrs even further into these subgroups:
Rollover Burrs
The most common type of burr, these are generally formed at exit, when the tool pushes/punches/pierces through and causes material to roll over the edge instead of shearing off.
Tear Burrs
Material tears or deforms instead of shearing off during machining.
Breakoff Burrs/Cut-off Burrs
Material falls off the workpiece leaving a burr behind.
Poisson Burrs
The machined material bulges outwards when the tool is applied to the workpiece under a downward force. This burr can also occur on the edge of the workpiece when the tool removes a layer from the surface laterally.
Take a Look
The illustrations below provide visual representation of what how some of these burrs are formed, and what they may look like.
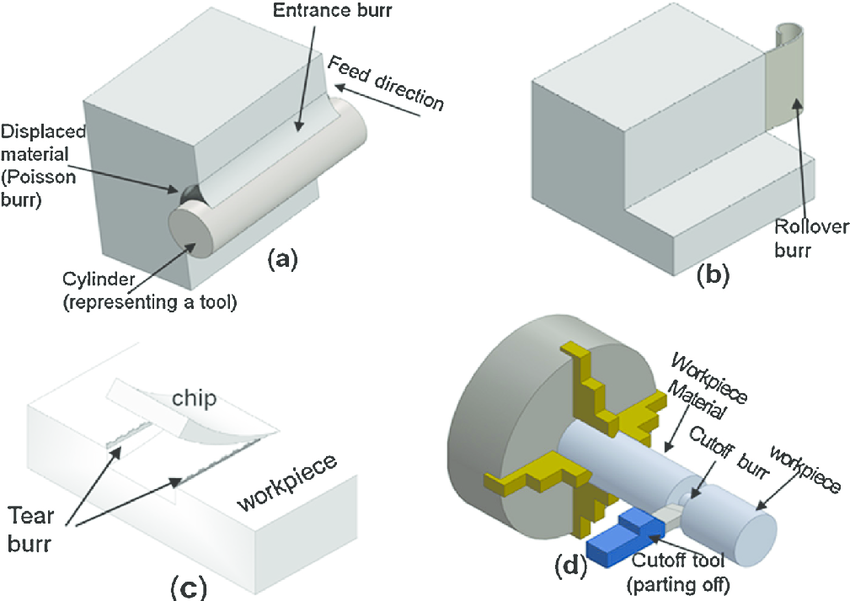
Fig. 2. Burr formation mechanism (a) Poisson burr (considering the cutting tool as a cylinder); (b) Rollover burr; (c) Tear burr; (d) Cut-off burr. Source: Adapted from [4]. Source: Researchgate.net