There are unique challenges in each industry when it comes to cleaning and deburring parts. Cycle times and cleaning specifications continue to get tighter. High pressure water jet deburring might be the right answer.
While it’s important to have dependable parts in all industries, it’s crucial for high-value pieces. For safety-focused industries like automotive, aerospace/aviation, and medical, missed burrs are not just inconvenient – they can make the difference between function and failure.
You want to make sure these crucial parts are fully deburred without compromising structural integrity.
For that reason, it’s important to consider deburring methods.
Many medical and aerospace parts are deburred by hand. Manual and/or mechanical deburring is effective but demands a significant amount of labor and time. This approach also relies on human operators, introducing the potential for human error and inconsistency. Furthermore, it often results in varying finished product quality for each individual piece. Compared to manual methods, automated deburring guarantees a consistently superior fit and finish for your parts, all within less time.
For parts with complex geometries, thermal deburring is another common choice, but its effectiveness in removing thicker burrs depends on the material and can lead to heat distortion and surface oxidation.
Comparatively, Thermal Energy Method (TEM) is not suitable for magnesium, titanium, or copper. Incoming parts must be free from chips, oils, and excess moisture. Additionally, TEM deburring leaves a layer of metallic oxide, requiring additional cleaning if the part is not going to be anodized, plated, or heat-treated.
Now, let’s look at High-Pressure Water Jet Deburring. It is exactly what it sounds like. Pressurized water is precisely focused via CNC control to remove burrs and chips in and around parts. Depending on the cleanliness required, your system would be configured with a submerged or an open-air environment. Open-air washing/deburring targets specific areas with the water jet, while submerged deburring ensures complete cleaning of the part, both internally and externally.
Given these points, a key advantage of water-jet deburring lies in its precision and repeatability. This eco-friendly process uses high-pressure water to effectively remove loose burrs and chips, even from deep holes, leaving the parts clean and free of debris.
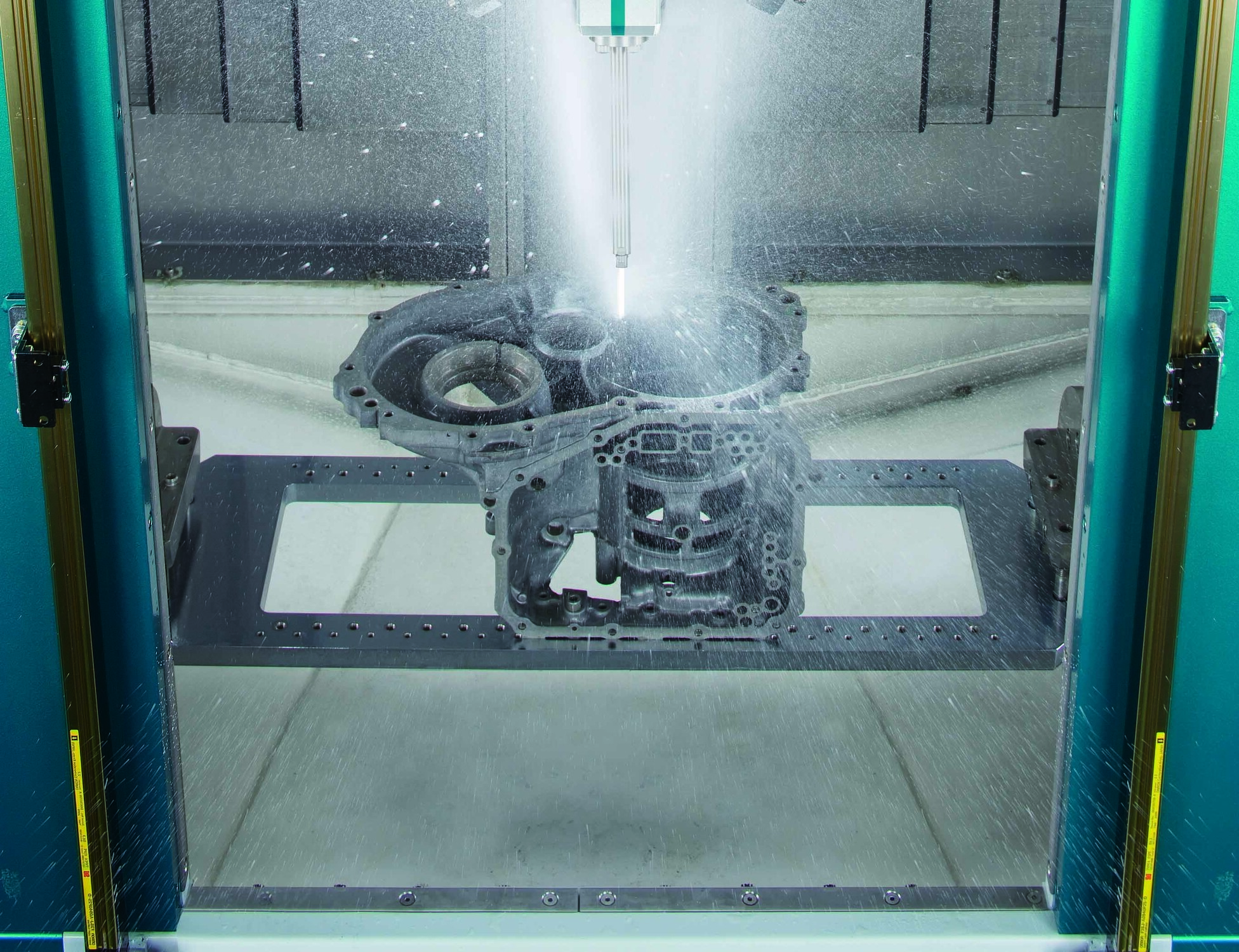
Highly pressurized water makes quick work of burrs.
Complex Parts, Cleaner Parts
Overall, high-pressure water is optimal for deburring in hard-to-reach areas. CNC control ensures precise positioning and penetration as the nozzles actively target cross holes, deep holes, and tap holes. Even workpieces with complex geometry are a great match for this method. Water jet deburring is also an ideal choice for parts that must avoid exposure to corrosive chemicals or heat.
It is deposit-free, residue-free, and leaves your parts cleaner, shortening the cleaning process.
So, what industries and applications are the best fit for High-Pressure Water Jet Deburring?
Automotive
Deburring with high pressure water means burr-free parts for both gas and electric vehicles. It’s a precise, targeted method that reaches tricky spots where other deburring techniques fall short. For example, it can effectively deburr the cross holes of a hydraulic manifold or cylinder block. This system seamlessly integrates into automotive production lines, and is compatible with gantry loaders, conveyors, and robot transfer systems. Automation streamlines high-volume processing, a necessity in automotive manufacturing. The combination of high-pressure water and CNC control packs the power and precision required to meet strict specifications.
Aerospace & Aviation
Aerospace manufacturing leaves no room for part failure. Burrs created during machining can hinder parts from fitting correctly, potentially leading to disastrous consequences with misaligned components. Burrs in cross holes can create blockages that impede the smooth flow of lubricants and fluids. There is no room for human error. Automation delivers better-finished end products in less time compared to manual processes.
Medical
Burrs pose a serious threat to the fit and function of medical implants and parts – an obvious risk to the health and safety of patients. These tiny imperfections can result in lacerations to patients or medical professionals. Many medical implants are produced via 3D printing, and high-pressure water jet deburring can remove supports, loose powder, and unwanted burrs that may crop up during other manufacturing processes, like die-cast molding. In the medical field, pristine, burr-free parts are an absolute necessity to minimize health risks.
Features and Add-ons
You can incorporate additional features into a water jet deburring process to save time and steps. These can include tooling, part-holding fixtures, filtration, part-identification systems, automation, and specific nozzles to optimize washing and deburring. Adding vacuum dryers and cleanliness evaluation systems can further improve efficiency and reduce cycle time.
Multiple parts can be run in the same machine with just a program change. Parts can be added or changed at the production line with simple programming, nozzles, and fixtures. The result is a system that meets your specs – effectively and efficiently.
Is it the Right Fit?
Wondering if high-pressure water jet deburring is the right method for you? In general, Class One through Class Three burrs can be removed by high-pressure water or by brush, assuming the burr passes the Lead Pencil Test*. Some Class Four burrs are removable as well.
*Lead Pencil Test. – If a burr can be removed by prodding it with a 0.7mm mechanical lead pencil tip (without breaking the lead), the burr is removable by high-pressure water or brush.
Ultimately, the best way to determine if it’s a match is to test your parts. We offer complete testing in our Wixom Technology Center to see if JCC is a fit for your manufacturing process.
Given it’s advantages, water jet deburring is an effective, CNC-controlled method for deburring metal parts with a high level of precision and repeatability. This method can both deburr and clean parts in one eco-friendly process, getting rid of loose burrs and chips even in deep holes – all while leaving the part clean and free of debris.
Get more information and insight into deburring – Click to read more from this Learning Series.