#30 Horizontal Compact Machining Center
SELF-CENTER
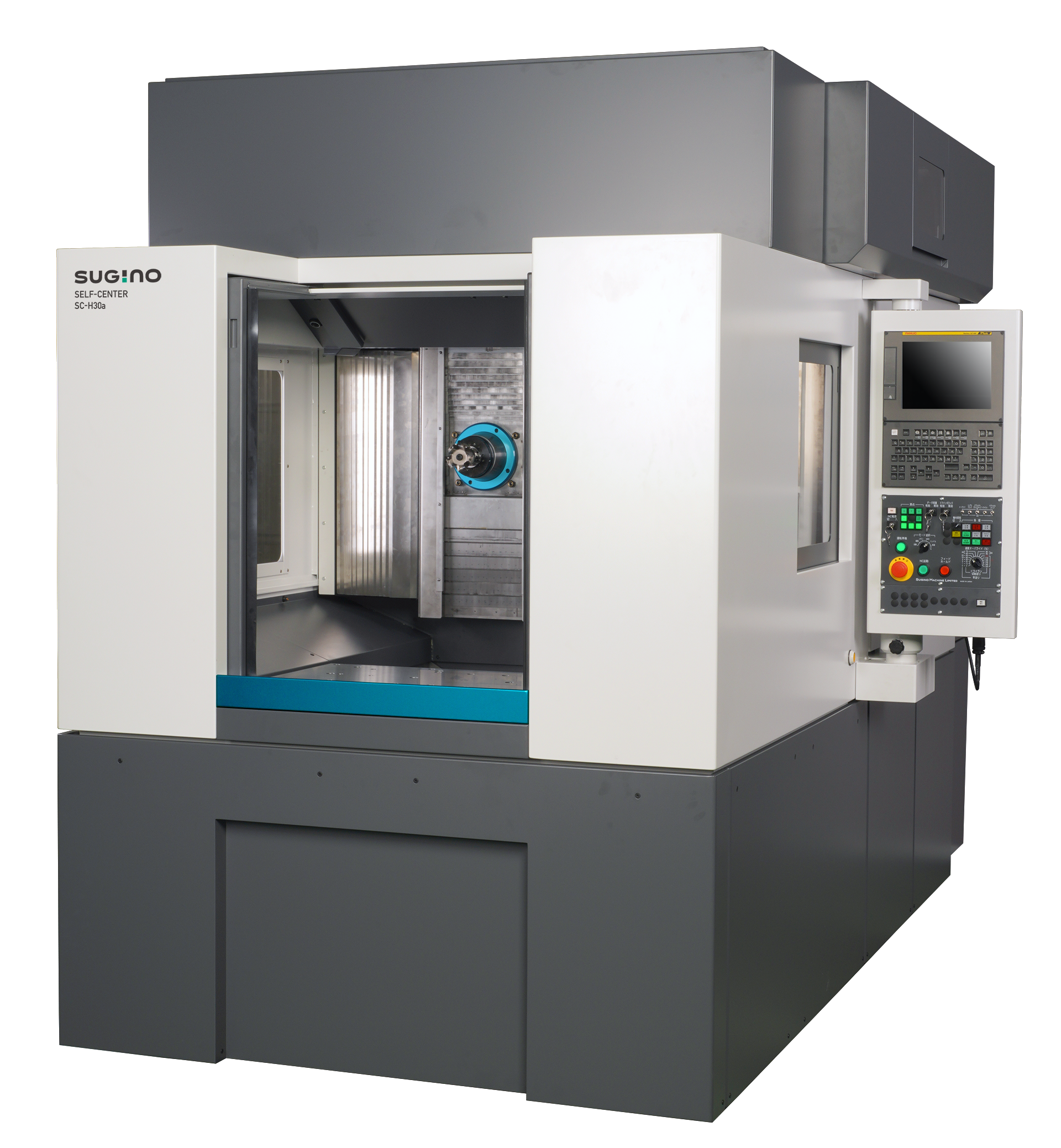
Designed with long unmanned processing in mind.
Since more than 90% of machine stoppages are caused by the accumulation of cutting chips, effective chip evacuation is essential for “lights-out” manufacturing.
The SC-H30a is engineered with enhanced chip evacuation to prevent work stoppages. With its improved center trough structure, chips don’t accumulate. Additionally, the machine holds up to 71 tools and, when combined with an automatic transport system, becomes ideal for long-term unmanned machining.
Machine Tour
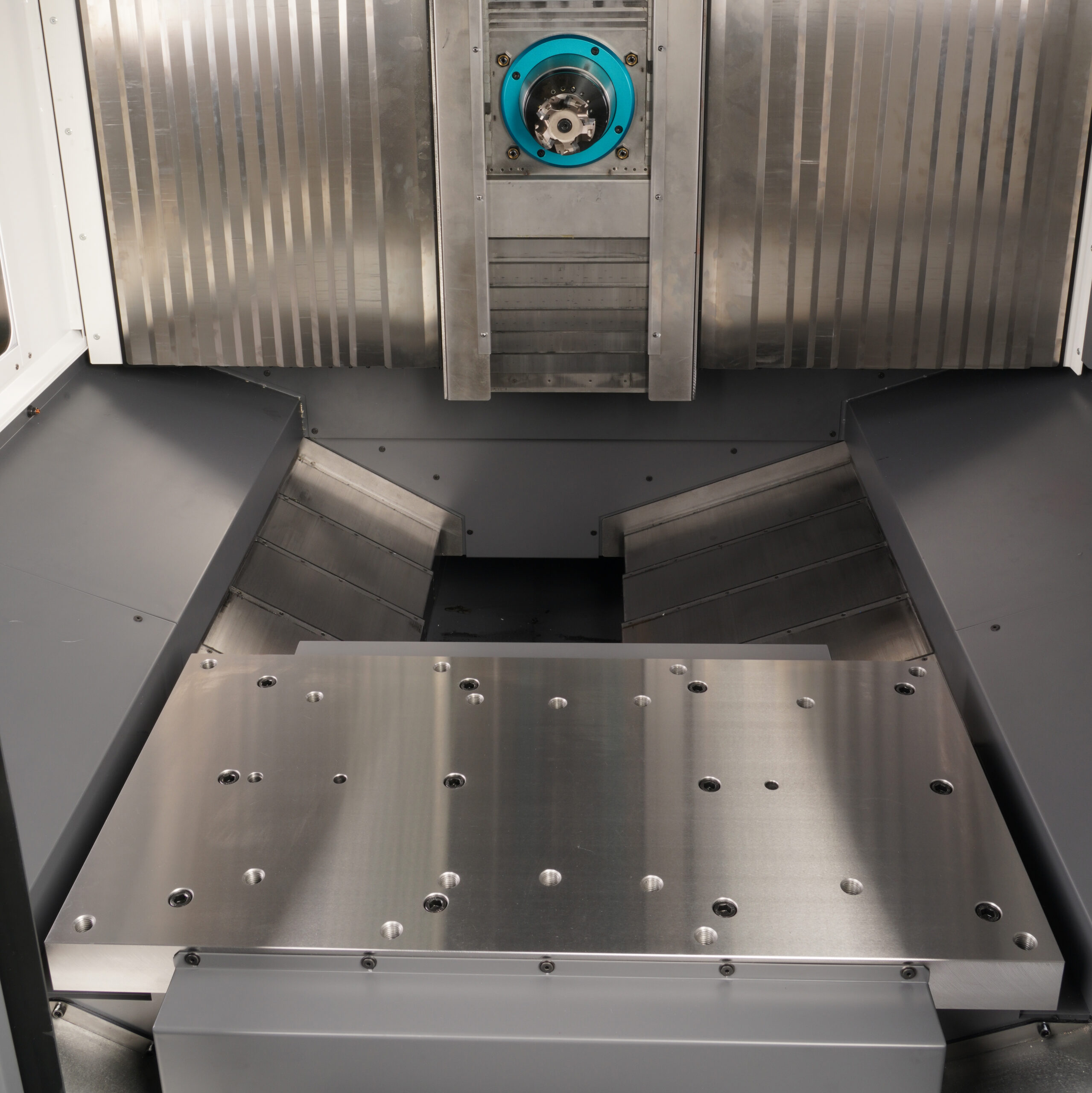
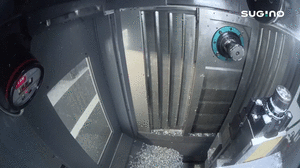
The center trough structure prevents chip accumulation and resulting work stoppages.
Processing area is separated from the tooling and mechanical storage.
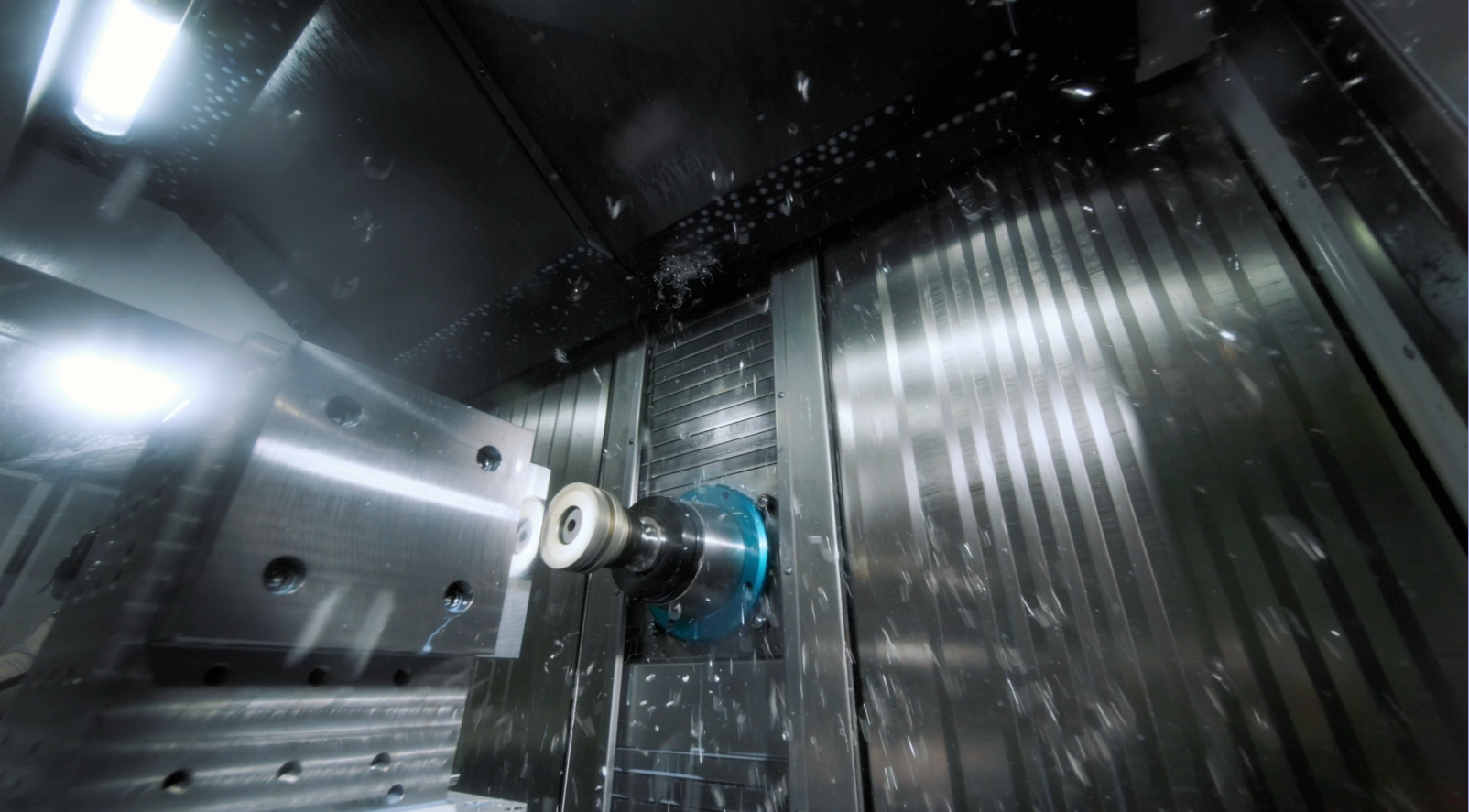
Outstanding Chip Evacuation

The horizontal spindle configuration allows chips to drop directly to the evacuation area for discharge, preventing accumulation on the workpiece or jig.
Easy to automate for your process.
Can be used in combination with a variety of automated transport systems.
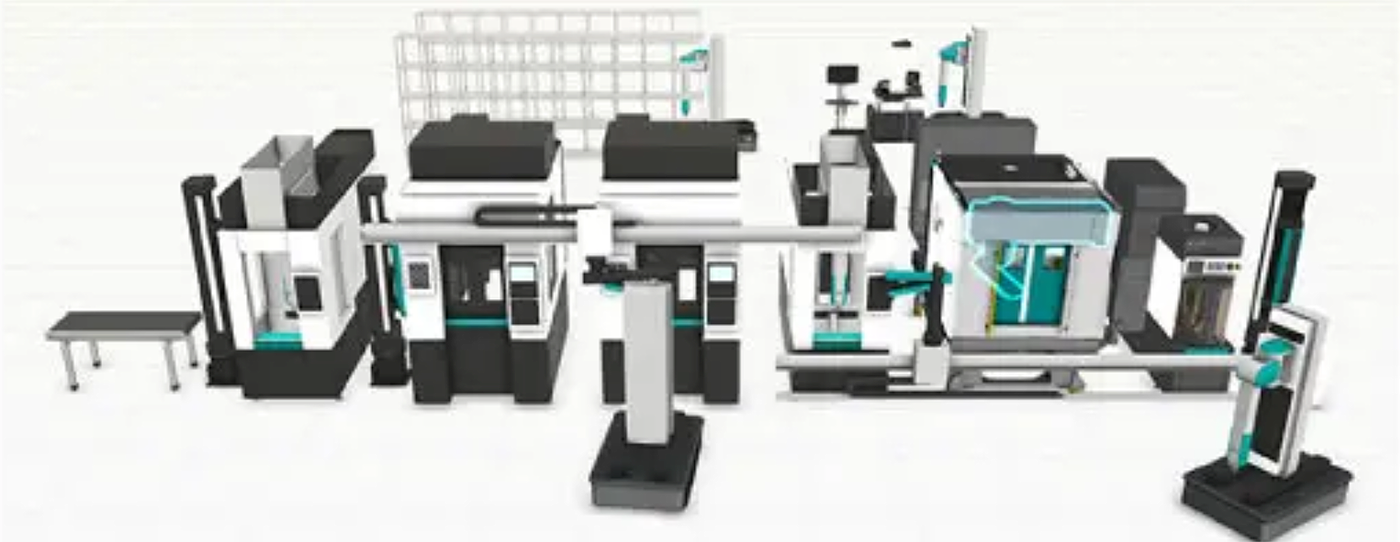
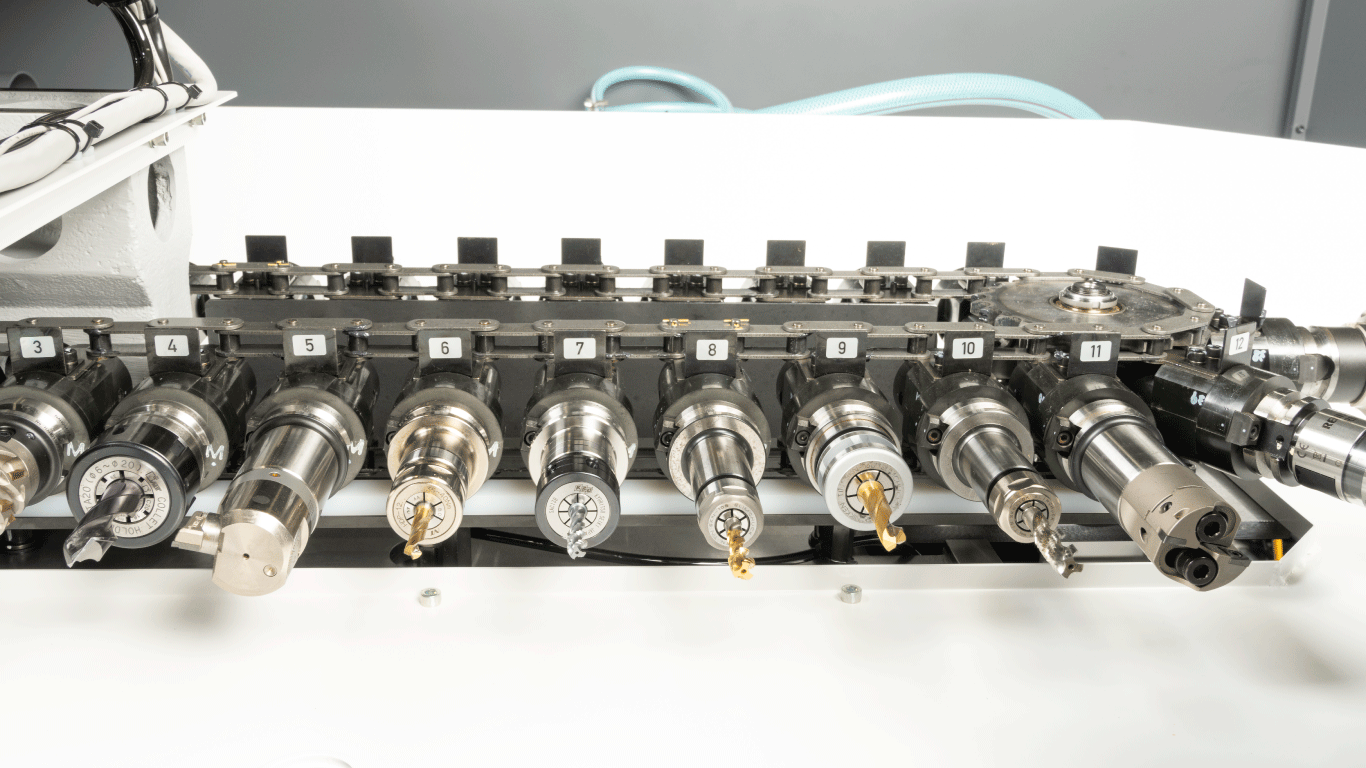
Holds up to 71 Tools
The SC-H30a has an extended tool capacity of up to 71 tools. Leaving room for spare tools to replace pieces as they break down reduces tool changeover time, keeps the line running, and prevents burrs from happening from worn-out tools.
Precision Deep Hole Drilling
The Z-axis table movement method enables high-precision deep-hole machining.
- Z-axis table movement & stroke 500mm
Because the main axis does not move, it achieves high straightness even in deep-hole processing
- Maximum tool length: Max.450mm
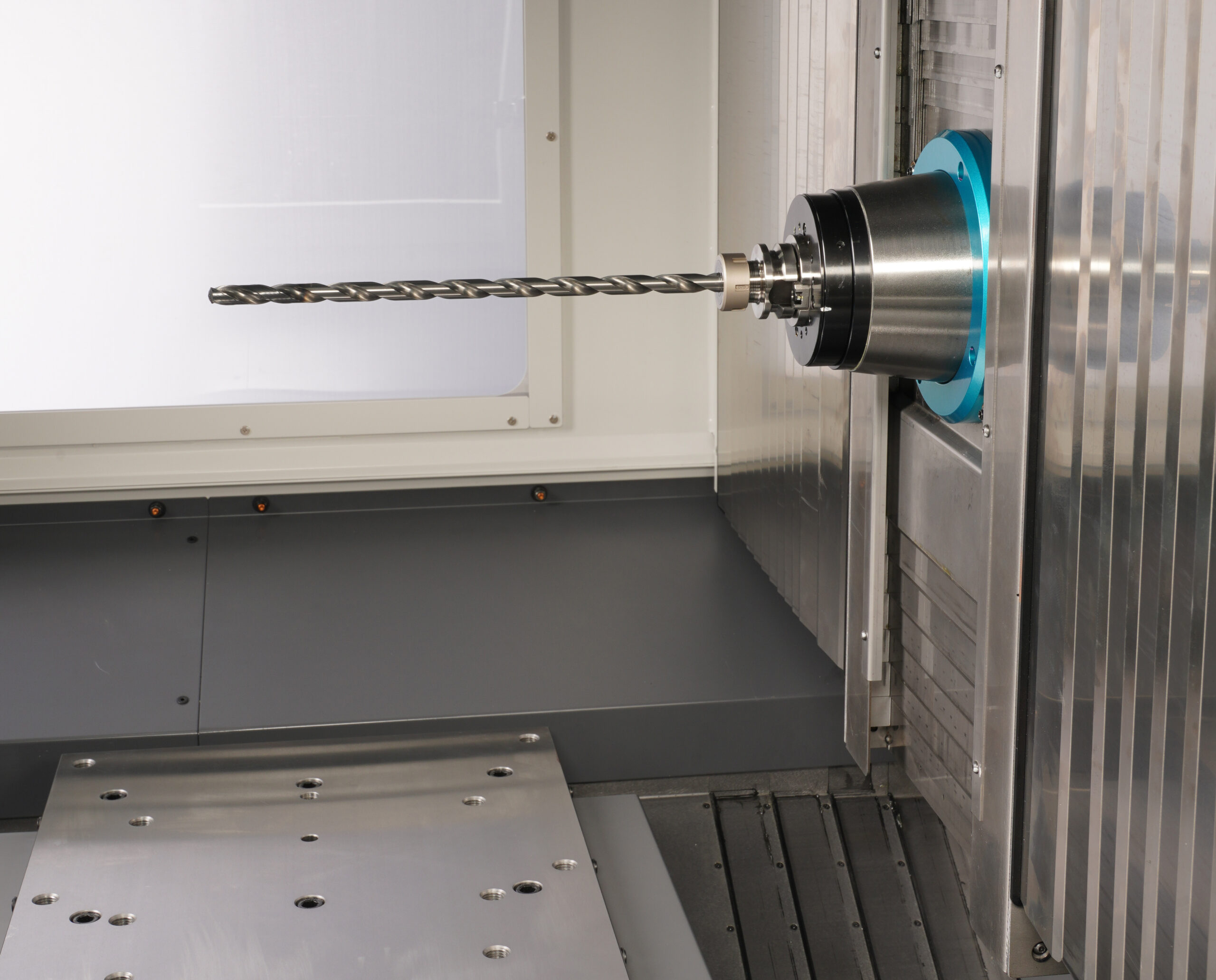
Get expert help and answers tailored to your specific production process and specs.
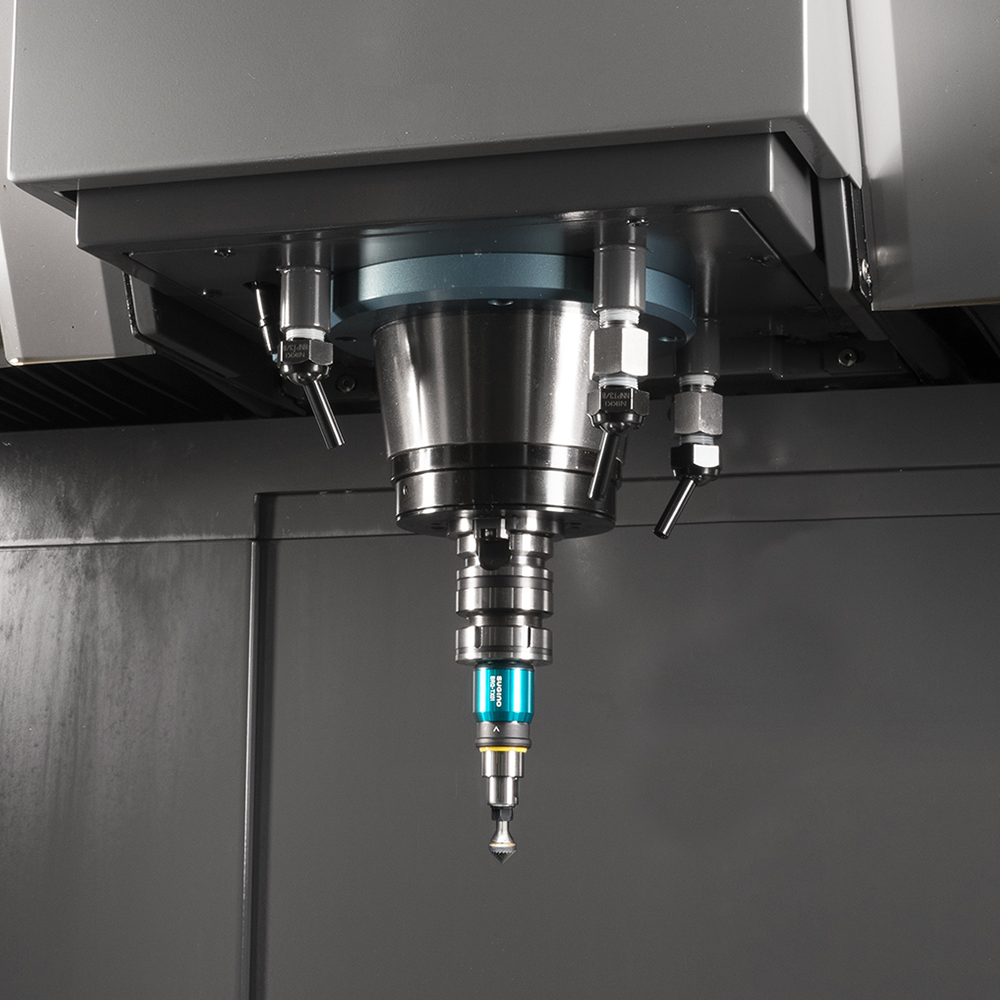
Deburring in a Machining Center?
Learn about the BRQ-TX01