We’re welcoming you to week 5 of our CNC and High-Pressure Water Jet Deburring Series and we’re taking a look at 15 benefits of implementing a CNC-based high-pressure cleaning and deburring process (if you missed our post about pumps and nozzles, make sure to catch up here).
One of the biggest benefits you’ll see when utilizing a CNC deburring and parts cleaning system is the improvement to consistency and repeatability in your process. But on top of that, the benefits are broad and touch many areas of production. And as most production plants already have CNC-based machines on the factory floor, adding a CNC-based cleaning process can be less costly when it comes to programming, training, and operation.
To start, let’s dig in to 15 ways that water jet deburring and cleaning can improve your production process:
Water Deburring / Cleaning has a Precision and Repeatability Advantage
It is human nature that no two people will achieve the same results when doing something by hand. With human operators comes a variety of results. CNC controlled water jet deburring maximizes precision and gives you repeatable, consistent results. Some examples include:
- Accuracy to 0.08 mm
- Ability to target or avoid areas on a part
- Repeatable, consistent results – without the same variation you’d find in manual deburring.
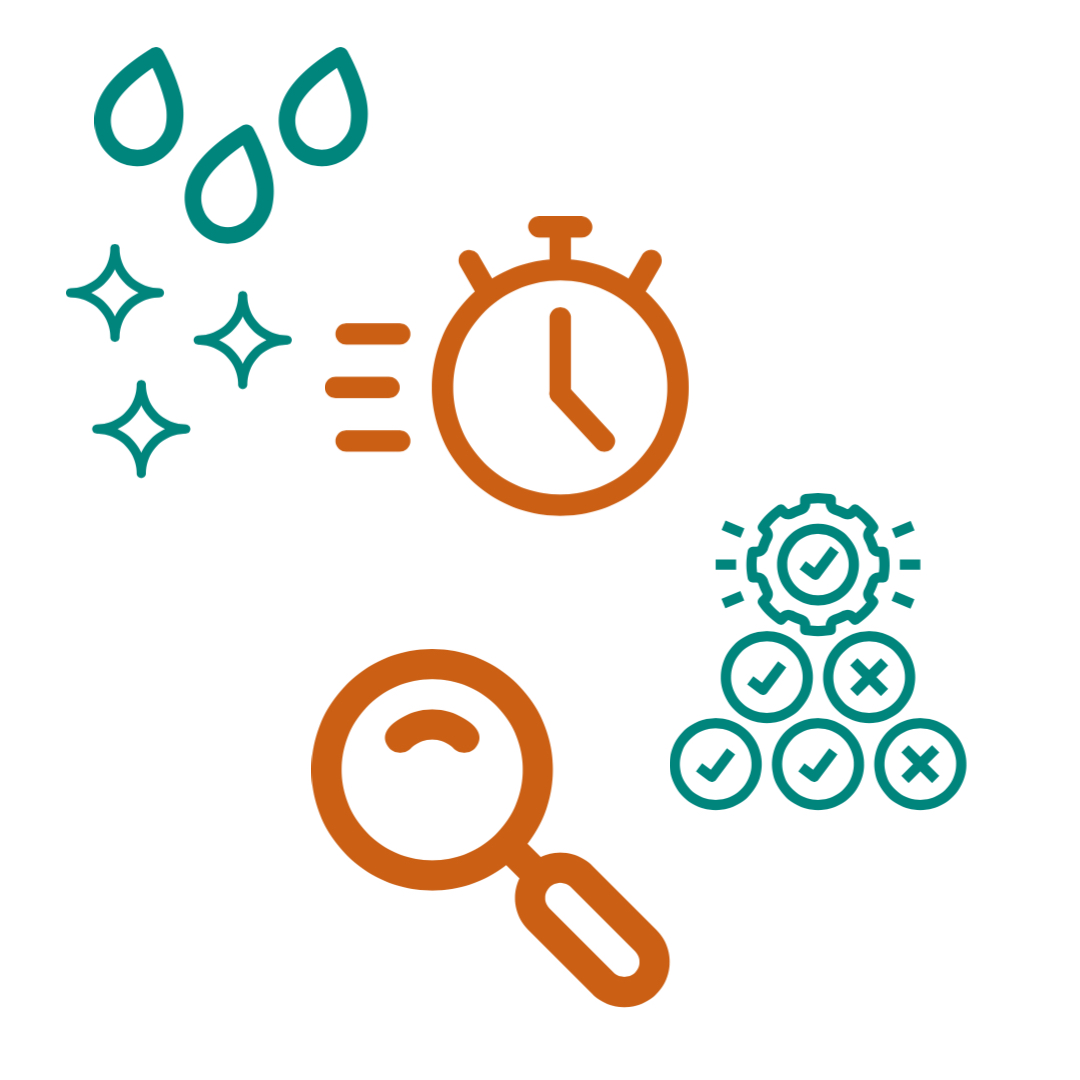
Meeting and Exceeding Specifications, Efficiency and Cycle Times
Next, it goes without saying that specs continue to get tighter, parts need to be cleaner, and it all needs to happen faster. Water jet deburring has the advantage, especially when paired with the right automation and machine and process type. Bottom line: you want to get more done, faster and better.
- When it comes to high cleanliness efficacy – specifications of sub 200 microns have been met.
- Cycle times can be reduced from traditional low-pressure cleaning methods with additional deburring or part-handling processes by using a single machine to do both.
- You can also reduce cycle times by running multiple parts (same) on a single fixture.
Flexibility and Adaptability for the Longer Term
There are more advantages with JCC in terms of adaptability when something in your process changes.
- Part-to-part change over time can be reduced with pallet or fixture changes and/or program changes.
- Tools or nozzle changes are extremely fast due to the use of a turret.
- There is no one-size-fits-all way to effectively clean and deburr parts. Machines that are flexible and easy to operate are highly useful in both hi-mix/lo-volume and lo-mix/hi-volume production.
- Multiple parts can be run in a single machine by changing fixtures and programs.
- A variety of nozzle options allow for different patterns and spray options to be used on a single part.
- Allows for ease of adding automation or integrating into a production line.
- IOT/smart machine ready – FIS or other factory production solutions.
- Multiple processes can be possible in the same machine – clean, deburr, dry, peen.
- Smaller footprints.
- Less costly to re-tool or queue additional parts – just fixtures, nozzles, and programming.
Make sure to join us next Wednesday to learn about the variety of add-ons and enhancements that can take your CNC-controlled deburring and/or parts cleaning to the next level.