Compact Vertical Machining Centers
#30 and #40
SELF-CENTER
We designed our small vertical machining centers to minimize installation space. With a device width of only 1,440 mm, the SC-V30a and V40a have the smallest footprint in the industry.
With improved movement speed and significantly shorter non-processing times, these compact units have solid rigidity and superior processing accuracy.
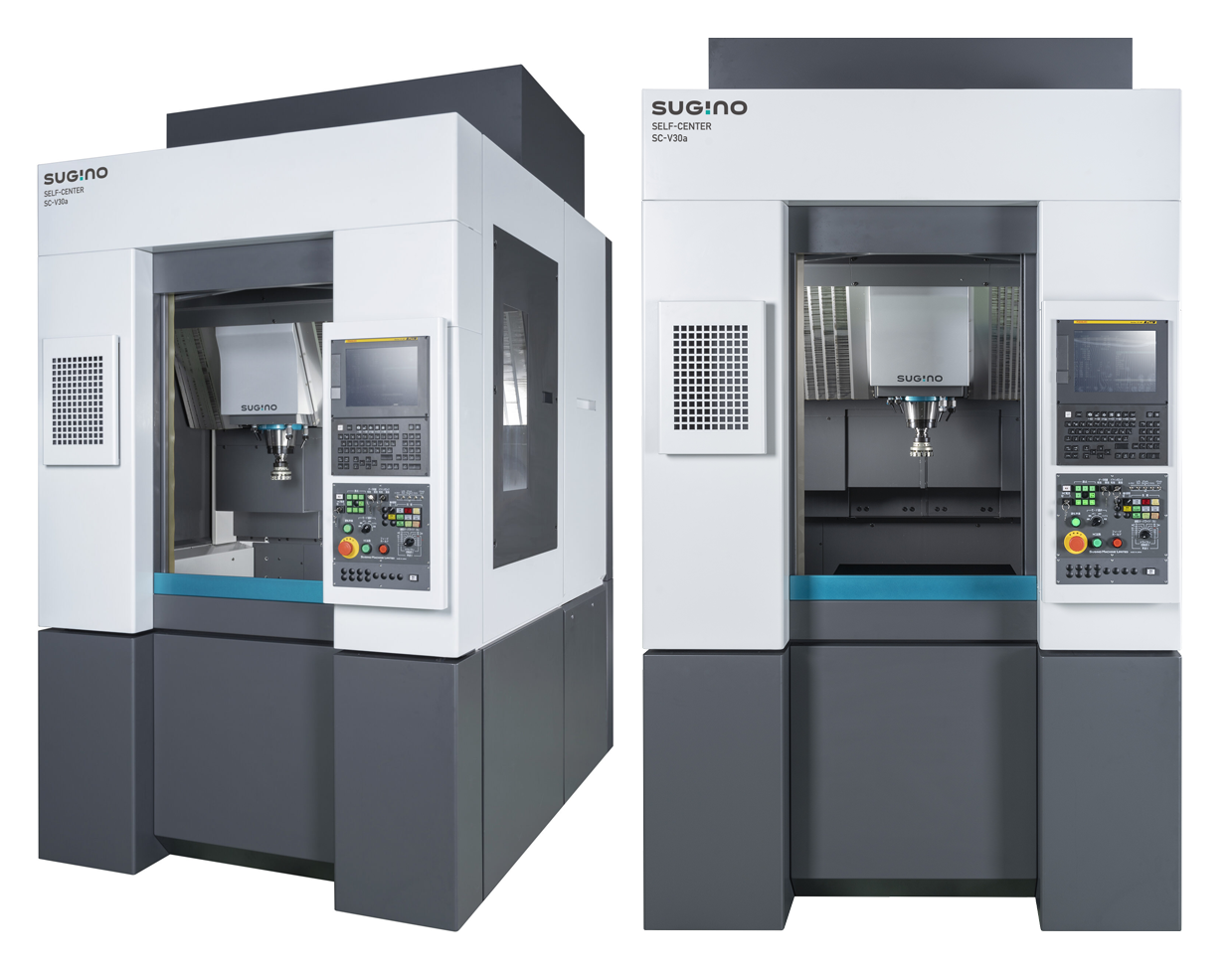
The industry's smallest #30 and #40 machining centers
With a footprint of only 1,440 x 3,245 mm, our Vertical Machining Centers make the most of your factory space.
For example, 4 compact SC-V40as can be installed in a space where only 3 #40 competitors’ machining centers fit.
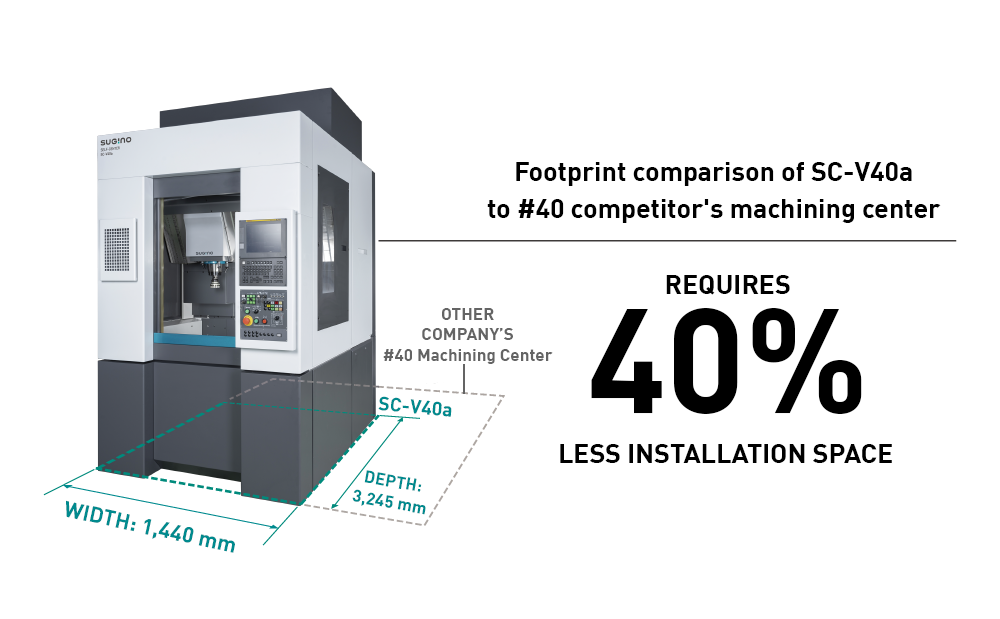
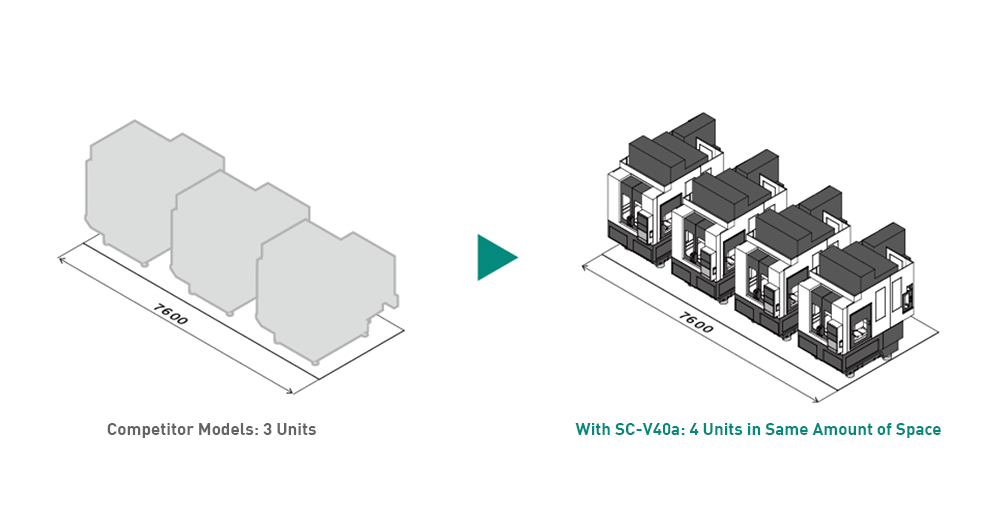
Large processing area
Despite the machine’s small 1,440mm width, the X-axis stroke is 700mm, for an overwhelmingly wide processing area. Large workpieces are processed in a small space, improving productivity per square foot.
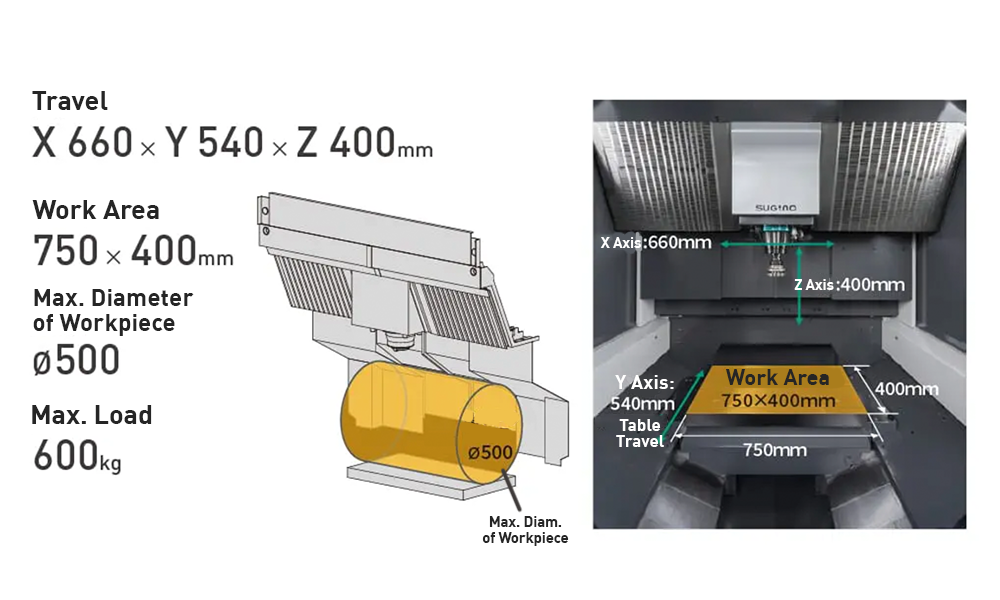
High-speed / short-cycle processing
The distance from the center of the spindle to the sliding surface is 1/3 that of conventional machines, reducing the torque received by the main body. Structural analysis and simulation through CAE have reduced the weight of the moving parts while maintaining rigidity.
These high-speed machining centers reduce non-cutting time by 25% compared to other companies' products. The cycle time is shortened for processing many types of workpieces such as aluminum, iron, resin, and brittle materials.
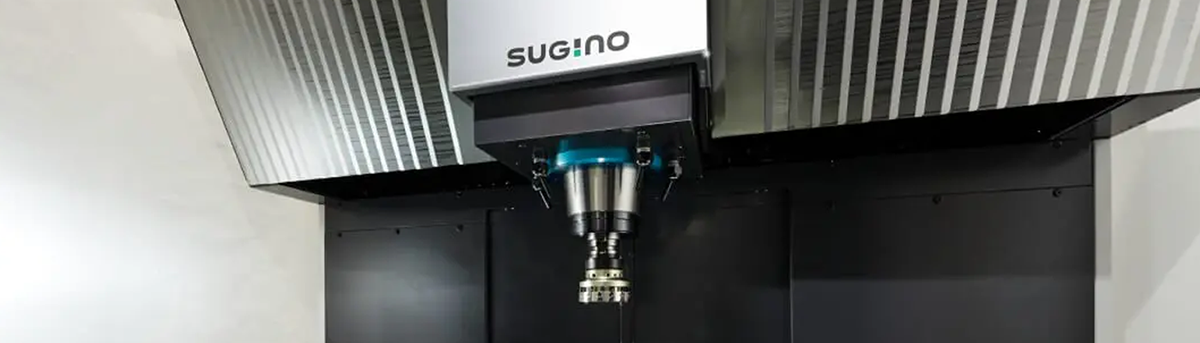
Enhanced Chip Evacuation
Reliably discharging and removing chips helps prevent work stoppages while boosting product quality and productivity.
To avoid issues caused by chips, the tool magazine and feed shaft are fully separated from the processing area. Additionally, the center trough increases chip evacuation, doubling the efficiency compared to conventional vertical machines. By eliminating pipes and wires in the processing area, we minimize the intrusion of chips and coolant into the drive unit, ensuring smoother operation.
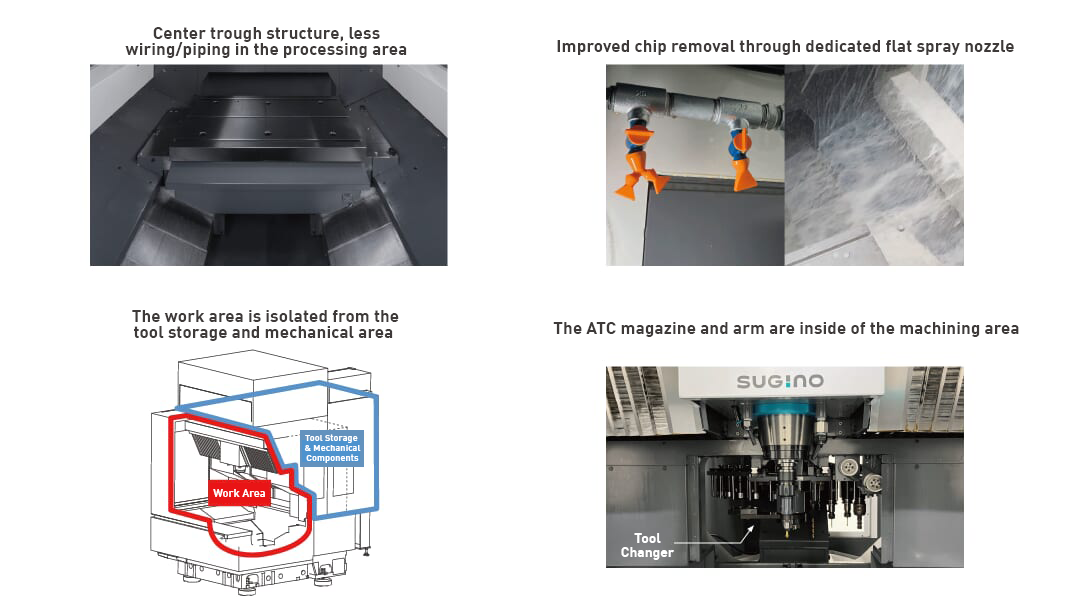
Environmentally Friendly and Sustainable
Our space-saving machining centers not only save space, but also reduce CO2 emissions.
The compact size requires smaller motors and moving parts, which minimizes the power needed to operate. Moreover, by using Sugino’s proprietary software to control motors and pumps, we further shorten operating time. As a result, overall power consumption drops by approximately 35% compared to other companies’ comparable machine centers.
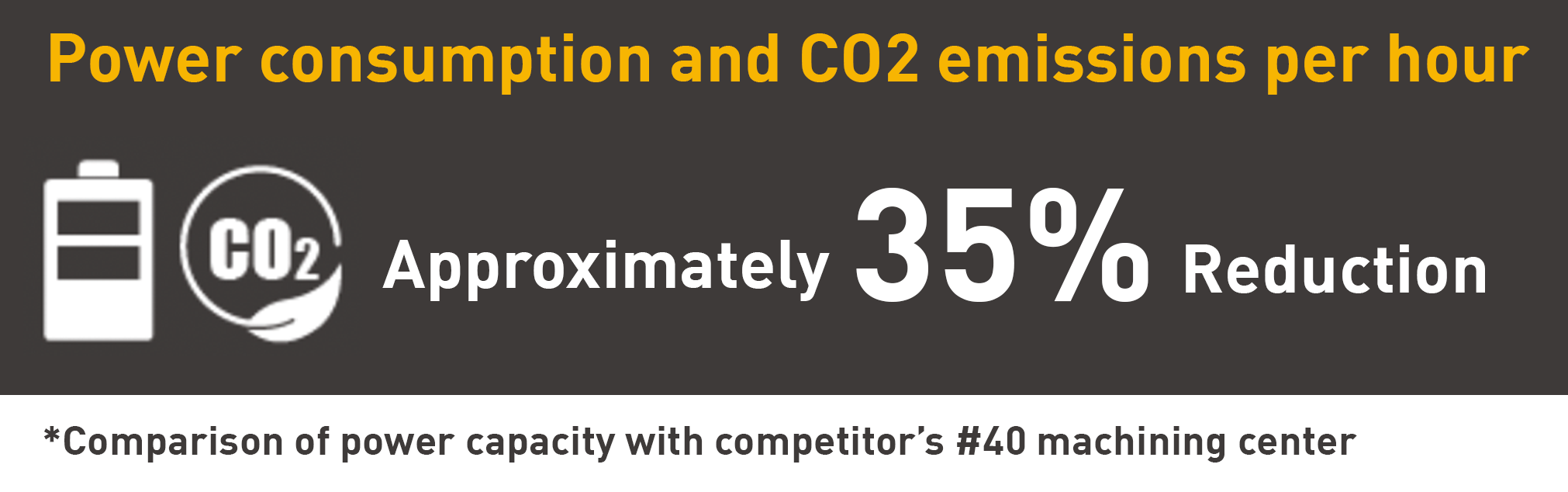
Development Background
Sugino’s Self-Center was born in 1986 and has a variety of machine configuration variations including vertical, horizontal, table-moving, and column-moving. The Self-Center series is ideal for customers who require small machines for small parts. Despite the small footprint, our vertical machine centers have an expanded processing area that can machine large aluminum EV-related parts.
Get expert help and answers tailored to your specific production process and specs.
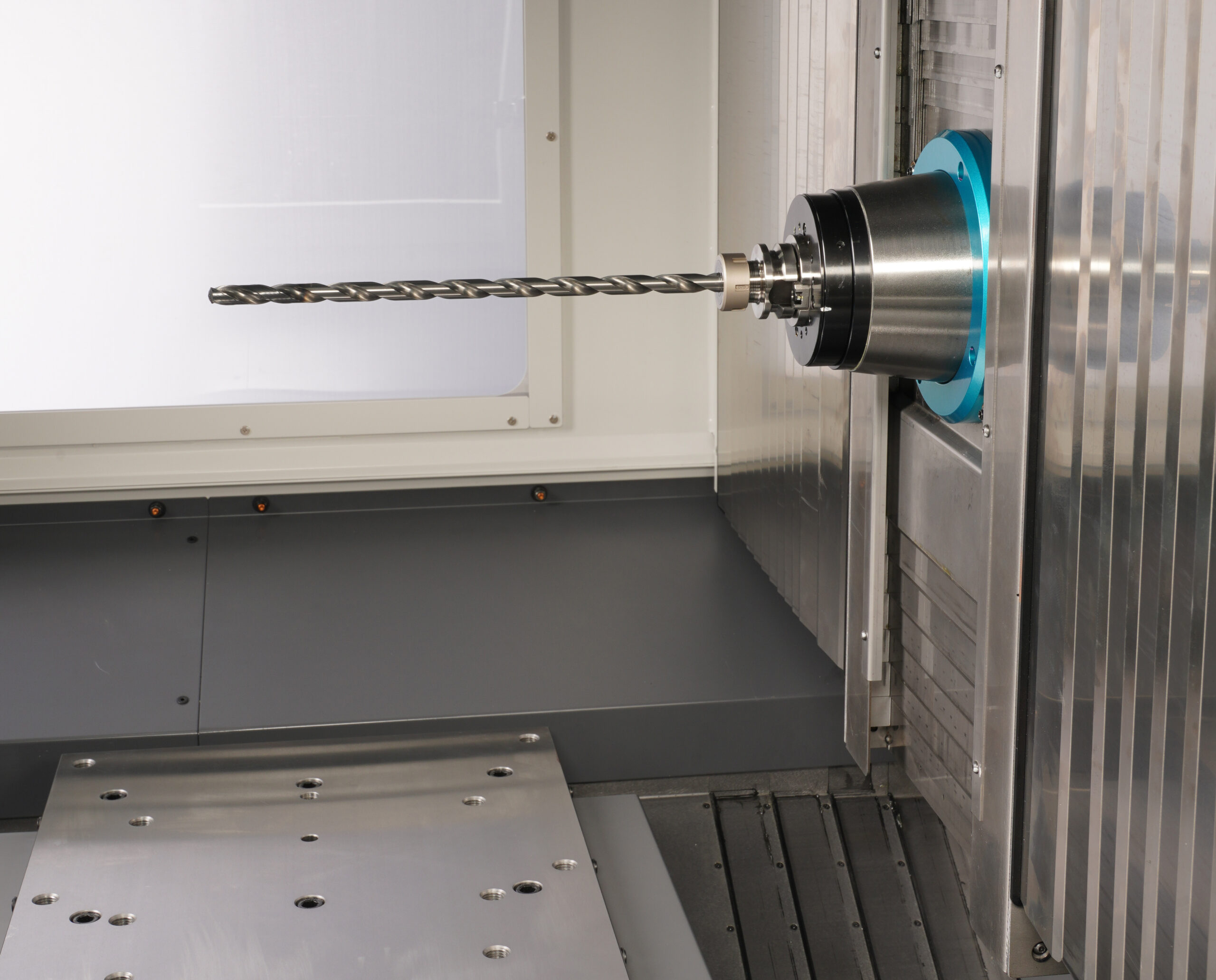
Looking for a Horizontal Machining Center?
Learn about the SC-H30a